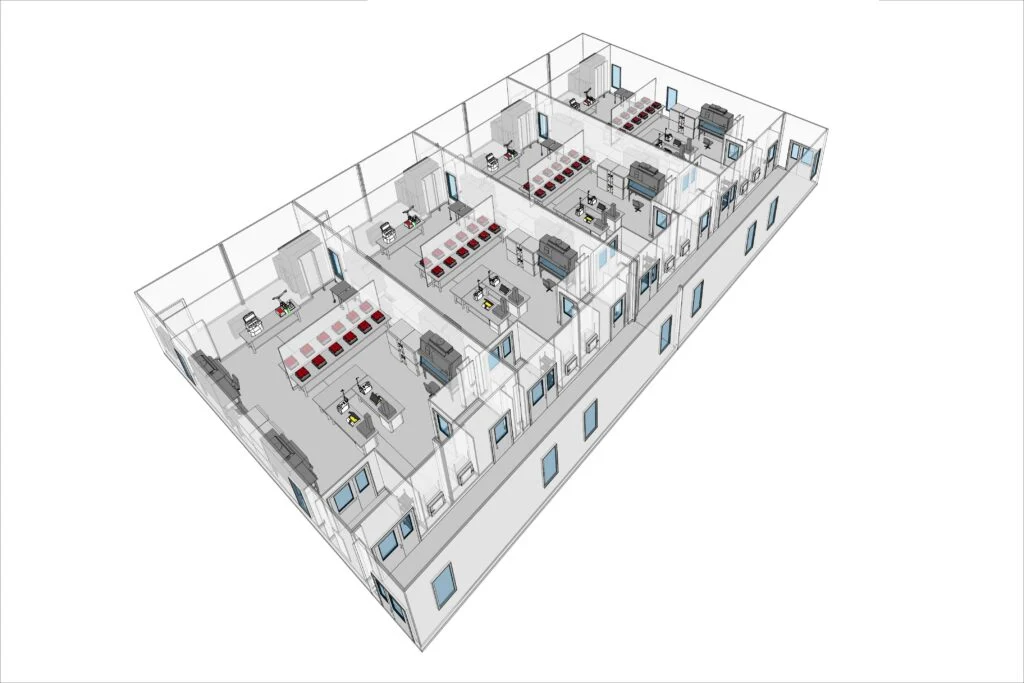
May 03, 2025
Discover the Essentials of Cleanroom Design for Optimal Facility Performance
Our guide details how innovative cleanroom design can transform your facility’s performance and regulatory compliance. In today’s competitive industries, maintaining stringent control over airborne particles is crucial. Our advanced systems combine robust HEPA or ULPA filtration with precise airflow management to create controlled environments that reduce contamination risks.
Understanding Cleanroom Architecture
Effective cleanroom architecture hinges on sophisticated filtration, laminar airflow, and uninterrupted environmental monitoring. By ensuring continuous oversight of temperature, humidity, and particle levels, our approach provides a sterile setting that supports critical manufacturing processes.
Core Components
- Air Filtration: Utilizing high-efficiency filters to capture microscopic particulates.
- Airflow Dynamics: Engineering laminar flows that minimize turbulence.
- Environmental Monitoring: Real-time surveillance of key parameters, ensuring steady compliance with standards such as ISO 14644 and GMP guidelines.
Industrial Applications
Industries including pharmaceuticals, semiconductors, and aerospace depend on rigorously controlled environments to secure product integrity and adhere to evolving regulatory demands. Our methods integrate smart automation and energy-conscious designs, supporting both high efficacy and sustainability.
Innovating with Modular Solutions
Our modular cleanroom systems redefine facility operations. Delivered as pre-fabricated units, our POD solutions enable rapid installation and flexible scalability. Integrated HVAC and adaptive monitoring systems ensure operational continuity while allowing you to adjust quickly to shifting production requirements.
Experience how precise cleanroom architecture can elevate your facility. Discover the advantages of our modular systems and see how our innovative approach sets new benchmarks in cleanroom performance and regulatory excellence.
Understanding Cleanroom Standards
Overview of Core Standards
Our cleanroom design adheres to internationally recognized protocols, including ISO 14644 and Good Manufacturing Practices (GMP). ISO 14644 establishes a comprehensive classification for air cleanliness by defining permissible airborne particle levels, while GMP governs quality control and ensures product consistency. These benchmarks directly inform our equipment selections, such as the implementation of HEPA or ULPA filtration, and shape the operational protocols that secure a contamination‐free environment.
Impact on Design Decisions
These standards drive critical design choices. ISO 14644 mandates specific filtration techniques and airflow configurations, ensuring that our systems deliver the required particle control. Simultaneously, GMP compliance requires rigorous documentation and validation protocols, prompting a streamlined facility layout that minimizes contamination risks while boosting operational efficiency. By aligning our design with these standards, we optimize cleanroom efficiency and enhance operator safety.
Compliance and Competitive Advantage
Strict adherence to these standards enables continuous monitoring of key environmental metrics—temperature, humidity, and particulate concentration—thus reducing contamination risks and ensuring rapid regulatory approval. This commitment not only safeguards product integrity but also fortifies stakeholder confidence and establishes a clear market differentiator.
G-CON’s Expertise in Compliant Design
At G-CON, we specialize in modular cleanroom solutions that meet and exceed ISO 14644 and GMP requirements. Our prefabricated POD systems integrate advanced HVAC, real-time monitoring, and adaptive control mechanisms, allowing for rapid deployment and tailored scalability. This ensures that your facility remains at the forefront of industry standards, delivering consistent performance and robust compliance while adapting to evolving market demands.
Why Invest in Cleanroom Design?
Superior Product Quality and Safety
Our cleanroom solutions are engineered to maintain a strictly controlled environment, crucial for preserving product integrity in critical sectors such as pharmaceuticals and biotechnology. Advanced HEPA filtration, precision airflow management, and adherence to ISO 14644 and GMP standards combine to minimize contamination risks and assure consistent quality in your manufacturing processes.
Enhanced Operational Efficiency
Our modular cleanroom designs streamline production by significantly reducing downtime and ensuring continuous compliance with evolving regulatory demands. These systems are designed for fast deployment and scalable expansion, enabling your facility to adapt swiftly to shifting production requirements while maintaining rigorous quality controls.
Sustainable Long-Term Savings
Investing in robust cleanroom infrastructure can lead to operational cost reductions over time. By effectively mitigating the risks of contamination and regulatory discrepancies, our prefabricated G-CON POD systems support a seamless installation process that minimizes interruptions and optimizes overall production cycles.
What Materials Are Best for Cleanroom Construction?
Essential Materials for Reliable Cleanroom Build
Selecting suitable materials is critical to achieve strict contamination control. For instance, surfaces constructed from stainless steel and high-density polyethylene offer non-shedding, easy-to-clean properties that reduce particulate accumulation in sensitive environments. Durable epoxy resin and vinyl composite flooring provide uniform, smooth finishes that inhibit microbial growth and endure rigorous cleaning protocols.
Construction Techniques Impacting Performance
The effectiveness of a cleanroom also depends on precise construction methods. Seamless flooring combined with coved corners minimizes areas where contaminants might accumulate, facilitating efficient cleaning routines. Modular wall systems enhance design flexibility, allowing adjustments as operational needs evolve while maintaining integrity under stringent conditions.
Material Selection and Long-Term Compliance
Choosing the right materials contributes directly to contamination prevention. Durable and non-porous surfaces curb microbial proliferation and chemical interactions that could compromise product quality. Our approach focuses on materials engineered for consistent performance even under frequent cleaning and harsh environmental conditions. This attention to durability supports long-term compliance with both ISO 14644 and GMP standards, while also addressing sustainability through reduced maintenance requirements.
Best Practices in Material Integration
Effective cleanroom construction incorporates advanced air filtration systems and finely controlled airflow designs. Prefabricated modular solutions, such as G-CON POD® Cleanrooms, streamline installation and improve operational adaptability. These systems integrate high-quality construction materials with precision design techniques to ensure optimal environmental control, thereby enhancing facility performance and supporting efficient, scalable production processes.
How to Maintain Optimal Conditions in a Cleanroom?
Airflow Design and Its Impact
Effective airflow design is central to ensuring the sterility and efficiency of cleanrooms. Our systems utilize laminar flow hoods and HEPA-filtered ventilation to maintain uniform air movement and suppress particle deposition. This active approach minimizes turbulence and establishes a controlled environment critical for pharmaceuticals and biotechnology.
Advanced Environmental Control
Our cleanrooms deploy sophisticated environmental control systems that regulate temperature, humidity, and pressure. Building Management Systems (BMS) and Environmental Monitoring Systems (EMS) deliver real-time data, enabling immediate adjustments and ensuring adherence to ISO 14644 and GMP guidelines. This setup guarantees that your facility continuously meets strict contamination and quality standards.
Proactive Maintenance and Calibration
Optimal conditions are maintained through proactive system management. Routine calibration of sensors and equipment secures accurate environmental readings, while scheduled maintenance keeps filtration and HVAC systems in peak condition. Integration with IoT devices supports predictive maintenance, reducing downtime and protecting product integrity.
Modular Integration for Superior Performance
Our G-CON POD solutions incorporate pre-validated environmental controls and integrated HVAC, providing rapid deployment with scalable flexibility. This modular design addresses specific industrial challenges by delivering adaptive airflow management and continuous environmental regulation—all designed to enhance operational efficiency, product quality, and regulatory confidence.
Which Cleanroom Design is Right for You?
Pre-fabricated Versus Traditional Cleanroom Solutions
Selecting the most effective cleanroom design is essential for your organization’s operational efficiency. Our modular cleanroom systems by G‑CON represent a modern, adaptable alternative to conventional construction. These pre‑fabricated POD units are engineered to minimize installation time and reduce disruptions while delivering industry‑leading performance.
Key Advantages of Modular Cleanrooms
- Scalability and Flexibility: Expand or reconfigure your cleanroom with ease to meet evolving production requirements.
- Regulatory Compliance: Our POD systems are designed to meet ISO 14644 and GMP standards, ensuring you achieve immediate compliance without additional testing delays.
- Operational Efficiency: Rapid deployment accelerates time‑to‑operation, reducing build schedules and enabling swift responses to change.
- Integrated Environmental Controls: Advanced HVAC and automated monitoring systems maintain consistent conditions, enhancing product quality and facility performance.
Making the Right Choice
When evaluating cleanroom options, consider deployment speed, ease of scalability, and the capacity to maintain strict regulatory standards. G‑CON’s modular cleanrooms offer a cost‑effective, dynamic solution that aligns with your current operations and adapts to future challenges in sectors such as pharmaceuticals, semiconductors, and aerospace.
Ensuring Regulatory Adherence in Cleanroom Design
Compliance and Its Impact
Our cleanroom design adheres rigorously to ISO 14644 and GMP standards, which define the parameters for air cleanliness, contamination control, and operational precision. These guidelines specify the performance of HEPA filtration and controlled airflow systems, ensuring that every environment remains within stringent limits to protect product integrity.
Cleanroom Validation Process
Validation confirms that each facility operates as specified through systematic testing including environmental control systems. Our process includes:
- Particle Count Assessments: Confirming that airborne particulate levels consistently meet established standards.
- Airflow Visualization: Demonstrating efficient laminar flow to reduce turbulence.
- Environmental Monitoring: Continuously tracking temperature, humidity, and particle concentration to support proactive adjustments.
Ensuring Operational Integrity
Validation is integral to sustaining an environment that meets rigorous regulatory standards. A robust validation protocol provides assurance of contamination control and reliable operational performance, thereby preserving product quality and safety.
Overcoming Compliance Challenges
Complex regulatory requirements and the need for uninterrupted monitoring are addressed by modular cleanroom POD systems. Our pre-validated solutions integrate adaptive HVAC controls and state-of-the-art environmental monitoring. These systems are engineered to easily scale with your production needs while maintaining compliance with evolving standards.
G‑CON’s Expertise in Regulatory Excellence
Our design and engineering process embeds compliance into every element of our systems. With integrated real‐time data monitoring and advanced calibration procedures, our modular cleanrooms offer consistent operational performance. By choosing our technology, you ensure that your facility navigates regulatory demands efficiently while remaining agile to future industry shifts.
Contact G-CON Today
Transform Your Facility with Advanced Modular Cleanrooms
At G‑CON, we design modular cleanroom systems that drive operational excellence and regulatory assurance. Our prevalidated POD solutions integrate robust HEPA and ULPA filtration, precise laminar flow control, and adaptive HVAC systems to create environments that consistently meet ISO 14644 and GMP requirements.
Our systems offer:
- Tailored Adaptability: Modular cleanrooms configured to your facility’s unique demands, ensuring seamless scalability and flexibility.
- Expedited Installation: Prefabricated POD units that reduce downtime and streamline integration into your operations.
- Regulatory Confidence: Prevalidated compliance protocols provide reliable assurance and simplify audit preparation.
Enhance your facility’s performance by consulting with our experts. Schedule a personalized discussion or a live demonstration to experience how our cutting-edge technology and smart controls can elevate your operational capabilities and future-proof your environment.
Key Considerations for Cleanroom Design
Influential Design Elements
Effective cleanroom planning hinges on precise material selection, accurate airflow design, and adherence to strict regulatory standards. Our approach integrates advanced prevalidated POD systems that combine non-shedding materials—such as stainless steel and high-density polyethylene—with sophisticated airflow management. These systems minimize particulate accumulation and microbial proliferation, ensuring an environment that supports critical manufacturing processes.
Regulatory Compliance and Environmental Control
Compliance with ISO 14644 and GMP is achieved through rigorous design protocols. Our prevalidated solutions incorporate calibrated HEPA or ULPA filtration systems and controlled laminar flows to maintain set airborne particle levels. Integrated environmental control systems continuously monitor temperature, humidity, and particulate concentration to ensure sustained compliance without redundancy. Such precision supports product integrity in sectors like pharmaceuticals, semiconductors, and aerospace.
Modular Cleanroom Advantages
Our modular cleanrooms offer rapid installation and scalable flexibility. Engineered for swift deployment, these pre-fabricated units minimize operational disruption by allowing dynamic reconfiguration based on evolving production needs. Adaptive HVAC integration and real-time sensor data ensure that each module maintains stable environmental conditions while meeting stringent regulatory criteria.
Operational Efficiency
Optimized cleanroom design not only enhances safety but also improves operational efficiency. By embedding automated control systems and real-time monitoring, our solutions reduce downtime and facilitate proactive maintenance. This strategic integration of cutting-edge technology and robust regulatory adherence provides a stable foundation for consistent quality and rapid response to market demands.
How Do Standards Shape Cleanroom Design?
ISO 14644 and GMP Fundamentals
ISO 14644 defines acceptable particle levels in a controlled environment, while GMP focuses on consistent product quality through stringent documentation and validation. These standards establish clear benchmarks that drive the design of cleanrooms, dictating precise filtration using HEPA or ULPA systems and the implementation of laminar airflow techniques.
Compliance Requirements and Operational Impact
Our design approach mandates the integration of certified filtration systems and calibrated monitoring instruments to meet these criteria. Mandatory validation protocols and systematic documentation influence layout decisions, ensuring that every element—from sensor placement to surface materials—supports optimal particle control and minimizes contamination risks.
Integration with Modular Cleanroom Technology
By incorporating prevalidated modular POD systems, our cleanroom solutions directly address industry challenges. The design incorporates adaptive HVAC controls and real-time sensor data to maintain regulated conditions, allowing for swift reconfiguration in response to shifting production needs. This integration not only fulfills regulatory demands but also enhances operational efficiency.
Distinct Advantages of Adhering to Standards
Meeting ISO 14644 and GMP requirements yields tangible benefits: reduced contamination risks, improved product integrity, and expedited audit processes. Facilities that conform to these standards inherently build stakeholder confidence through streamlined maintenance and scalability.
G‑CON Expertise
Our modular cleanrooms exemplify the synthesis of regulatory precision with dynamic facility design. Engineered to seamlessly balance compliance with scalability, our systems deliver controlled, adaptive environments that support ongoing operational excellence.
Why Choose Modular Cleanroom Design?
Flexibility and Scalability
Our G‑CON POD® Cleanrooms provide a reconfigurable solution that evolves with your facility’s demands. These prefabricated units can be designed or modified to accommodate increased production or altered workflows, ensuring a solution that adjusts as your operational needs change.
Streamlined Construction and Cost Efficiency
Modular cleanrooms significantly reduce on-site construction, curtailing labor expenses and shortening build schedules. With a faster deployment cycle, your facility begins operations in weeks rather than months, allowing you to direct resources toward growth and innovation.
Optimized Operational Performance
Integrated environmental control systems maintain precise regulation of temperature, humidity, and airflow. This active management ensures consistent production quality and minimizes downtime, contributing to a stable and resilient operating environment.
Strategic Market Advantage
Adopting our modular solutions reinforces your ability to meet shifting regulatory requirements and industry standards, including ISO 14644 and GMP. This adaptability enhances your reputation for quality and positions your facility to respond proactively to market changes.
How Does Airflow Impact Cleanroom Performance?
Critical Role of Airflow Management
Effective airflow management maintains the sterility and efficiency of cleanroom environments. Uniform air distribution through engineered laminar flow systems and HEPA-filtered ventilation minimizes particulate accumulation and restricts contaminant migration. This precision enhances contamination control and supports optimal operational efficiency in sectors such as pharmaceuticals, biotechnology, and semiconductors.
Advanced Techniques for Environmental Stability
Our cleanroom systems integrate advanced HVAC units and calibrated sensors to precisely regulate temperature, humidity, and particulate levels. Regular sensor calibration and scheduled preventive maintenance ensure that real-time data, transmitted via IoT networks, informs automated adjustments. Such measures facilitate predictive maintenance and reduce unexpected downtime while maintaining robust environmental control.
Optimizing Contamination Control
Engineered airflow reduces turbulence and confines particle circulation, thereby preserving process integrity and product quality. Automated environmental adjustments, driven by continuous sensor feedback, ensure that critical parameters remain within target ranges regardless of operational fluctuations.
Integration with G‑CON Modular Solutions
Our modular cleanroom systems, including G‑CON POD® Cleanrooms, combine rapid installation with comprehensive environmental regulation. Pre-validated HVAC integration and real-time sensor networks enable these systems to adjust swiftly to evolving production demands. This robust design sustains strict regulatory compliance and boosts scalability and cost efficiency during facility expansion.
By harnessing precise airflow management with advanced environmental monitoring, our solutions secure superior contamination control and operational resilience. This technical rigor empowers your facility to consistently meet stringent industry standards while adapting seamlessly to evolving challenges.
What Materials Ensure Effective Cleanroom Design?
Our approach to cleanroom construction centers on selecting materials that deliver enduring contamination control and long-term operational efficiency. We utilize high-quality stainless steel and high-density polyethylene (HDPE) for surfaces that resist particle accumulation and facilitate straightforward cleaning. Epoxy and vinyl flooring create seamless, durable surfaces engineered to inhibit microbial growth and withstand rigorous maintenance routines.
The stability of a cleanroom environment relies on non-porous materials that minimize the risk of chemical reactions and microbial proliferation. In industries such as pharmaceuticals and biotechnology, material integrity is critical to preserving product quality. Our POD surfaces maintain their performance even after repeated cleaning cycles and exposure to harsh conditions, ensuring both compliance with standards like ISO 14644 and GMP, and affordable lifecycle maintenance.
Advanced construction techniques further enhance cleanroom performance. Seamless flooring with curved, coved corners reduces particle traps and simplifies decontamination, while modular wall systems provide flexibility for future reconfigurations. Prefabricated POD systems, such as our G‑CON POD® Cleanrooms, integrate controlled airflow designs and HEPA filtration systems to maintain precise, adaptive environmental control.
By selecting materials that are both robust and sustainable, your facility can achieve superior contamination control and operational resilience without compromising on regulatory compliance.
Achieving Compliance and Validation in Cleanroom Design
Upholding Standards for Superior Performance
Maintaining adherence to ISO 14644 and GMP is fundamental for our cleanroom designs. These standards dictate the benchmarks for air quality, contamination control, and operational protocols. By rigorously applying certified filtration and controlled airflow techniques, our systems safeguard product integrity across pharmaceutical and biotechnological applications.
Streamlined Validation Protocols
Our validation process rigorously tests air filtration, airflow dynamics, and environmental control. We verify air quality through comprehensive particle counts, assess laminar flow to minimize turbulence, and monitor temperature, humidity, and particulate levels using real-time sensor data. Such stringent testing confirms that our modular POD systems consistently operate within established parameters.
Benefits of Adhering to Regulatory Standards
When your facility meets these standards, you achieve enhanced operational efficiency and reduced risk of contamination. Consistent regulatory compliance not only builds stakeholder trust but also positions your operations ahead of market challenges. Our approach integrates prevalidated design elements that support swift certification, ensuring minimal disruption and optimal productivity.
Addressing Challenges and Optimizing Design
We recognize that complex regulatory demands and continuous parameter verification can complicate cleanroom operations. Our modular cleanroom solutions simplify this process by incorporating adaptive HVAC systems and integrated control mechanisms. This design philosophy minimizes repetitive validation while ensuring every component—from material selection to airflow configuration—meets rigorous standards.
By embedding advanced testing protocols and sustainable design practices, we provide a robust framework that meets both current and future industry demands while enhancing your facility’s competitive edge.