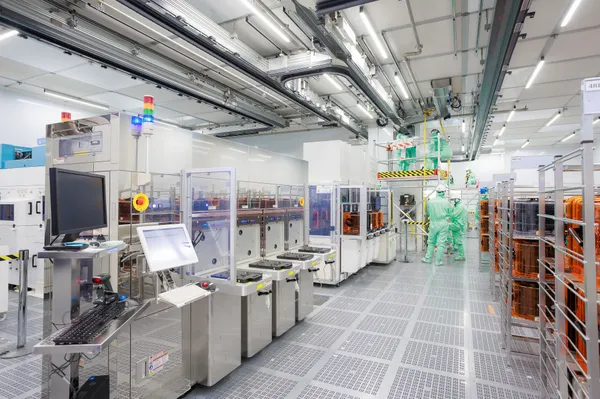
May 07, 2025
Understanding GMP Cleanroom Standards for Optimal Compliance
Mastering the Fundamentals
At G‑CON, our modular cleanrooms are designed to meet the exacting standards of GMP cleanroom compliance. Our systems adhere to globally recognized directives—ensuring aseptic environments, rigorous contaminant control, and precise environmental stability. What are GMP cleanroom standards? They are a detailed framework governing processes such as air particulate monitoring, process validation, and quality assurance, all critical for streamlined, secure production environments.
Elevating Manufacturing Efficiency
We engineer our cleanrooms to optimize both production quality and operational efficiency. Our G‑CON POD systems fuse state‑of‑the‑art BMS and EMS(optional) integrations with automation acceptance testing. This smart integration improves product quality while mitigating operational risks. Consider how structured environmental controls directly enhance your production process, reduce downtime, and preempt regulatory challenges. Our designs not only comply with current FDA21CFR11 and GMP guidelines, but also anticipate future regulatory evolution.
GMP Cleanroom Standards: A Foundation for Operational Excellence
Maintaining Regulatory Discipline
Our modular cleanroom systems strictly adhere to internationally recognized GMP requirements. We design every unit to deliver impeccable product safety and manufacturing reliability. By meeting established protocols for aseptic processing, contaminant control, and environmental consistency, our systems ensure your production facility operates with compliance while minimizing risks.
Enhancing Environmental Quality
Engineered for exact particle control and cleanroom validation, our advanced G‑CON POD configurations transform traditional spaces into high-performance environments. These systems:
- Undergo efficient factory acceptance testing (FAT)
- Integrate intelligent building management (BMS) and environmental management systems (EMS)
- Maintain consistent air cleanliness per ISO14644 standards
Such attention to critical parameters cuts helps your facility meet regulatory requirements.
Strategic Operational Benefits
Our modular designs empower your facility to adjust smoothly to emerging regulatory demands, scale operations promptly, and maintain continuous compliance. This approach minimizes disruption, controls operational costs, and improves overall market responsiveness. With our cleanroom systems, you secure a resilient, future‑ready production environment that safeguards your investments and supports sustainable innovation.
How Can You Ensure GMP Compliance in Your Cleanroom?
Start With a Thorough Assessment
Evaluate your facility against recognized GMP benchmarks by conducting a detailed gap analysis. Examine existing environmental controls, particle monitoring systems, and workflow procedures. Review standards such as ISO14644, FDA21CFR11, and GMP to confirm that your processes meet rigorous sterility and quality requirements.
Implement Targeted Compliance Strategies
Transform assessment into action by executing precise compliance measures.
Optimize Design and Integration
Our G‑CON POD systems incorporate real-time BMS and EMS technology, enabling an efficient layout that enhances air quality and aseptic processing. Develop clear, measurable protocols that mirror validated manufacturing practices demanded by global standards.
Activate Technological Controls
Install smart sensors, HEPA filtration, and continuous monitoring devices to maintain environmental stability. Advanced software captures and analyzes quality data, permitting immediate adjustments and preventing potential deviations.
Maintain Continuous Monitoring and Integrity
Sustain compliance through proactive measures. Conduct regular internal audits and invite independent inspections to ensure adherence to evolving standards. Employ a recursive feedback loop to refine operational protocols continuously. This dynamic approach converts regulatory challenges into strengths, ensuring your facility remains agile, efficient, and future‑ready.
GMP Cleanroom Standards: Essential Elements and G‑CON Integration
Core Pillars of Compliance
Our modular cleanrooms are engineered to secure product integrity, minimize contamination, and meet global regulatory benchmarks. At G‑CON, we design our systems with integrated quality management that uses structured process controls and continuous audits to ensure uniform output.
Advanced Environmental Controls
We incorporate real‑time air quality monitoring aligned with ISO14644 standards. Automated sensor networks and precise particle count assessments ensure that the environment remains within strict contamination thresholds. This digital control not only verifies performance continuously but also enables swift responses to deviations.
Rigorous Personnel Protocols
Our training programs instill best practices in aseptic techniques, effective gowning procedures, and contamination risk management. Comprehensive checklists and regular drills maintain high operational consistency, reducing the likelihood of process errors during critical manufacturing stages.
Robust Documentation and Data Integrity
Detailed recordkeeping, complete with validated process logs and secure electronic audit trails, satisfies FDA21CFR11 requirements. Our digital systems streamline data management, making internal reviews and external certifications more efficient and reliable.
Integrated Value Delivery
At G‑CON, our approach converts technical precision into operational strength. Advanced BMS and EMS integrations, embedded within each prefabricated unit, enable dynamic environmental control and adaptive training frameworks. By uniting these core elements through smart automation and precise digital validation, we transform regulatory demands into a competitive advantage that drives manufacturing excellence.
When Is It Time to Revise Your Cleanroom Standards?
Our modular cleanroom systems at G‑CON evolve with your operational dynamics and shifting regulatory demands. A well‐timed update ensures that your facility not only meets compliance requirements but also capitalizes on technological innovations.
Key Revision Indicators
- Environmental Shifts: Rising particle counts or changes in airflow dynamics suggest that current monitoring may not capture all variables.
- Operational Disruptions: Regular facility audits or sensor irregularities indicate that process protocols need refinement.
- Regulatory Reviews: Both scheduled evaluations and unannounced inspections often reveal gaps between existing standards and the latest compliance benchmarks.
Drivers for Change
Recent advancements in sensor technology and data analytics enable precise, real‑time assessments of environmental conditions. Our systems incorporate state‑of‑the‑art BMS and EMS modules that continuously evaluate air quality according to ISO14644 and GMP guidelines. Updates become necessary when new regulatory measures are introduced or when extended audit criteria prompt system recalibration.
Best Practices for Revision
- Periodic Reviews: Establish a routine reassessment cycle, supported by real‑time alerts that flag performance deviations.
- Integrated Feedback: Utilize our recursive improvement framework to analyze historical performance and predict upcoming trends.
- Expert Collaboration: Work with industry specialists to benchmark your facility against evolving best practices, ensuring your processes remain robust and compliant.
A proactive, data‑driven approach to revising cleanroom standards transforms challenges into strategic growth, ensuring your facility operates at peak efficiency and maintains a competitive edge.
Where Can You Access Trusted GMP Compliance Resources?
Our commitment to strict GMP compliance is backed by an extensive network of credible resources that keep your operations at the forefront of regulatory excellence.
Official Regulatory Platforms
Access guidelines and protocols directly from authoritative bodies. Explore the websites of agencies such as the FDA and EMA for detailed inspection criteria, updated protocols, and illustrative case studies. Public health portals also provide centralized repositories where amendments to GMP and related standards are posted regularly.
Industry Associations and Technical Publications
Professional organizations like ISPE and ICH publish thoroughly reviewed white papers, regulatory updates, and comprehensive compliance checklists. Renowned trade journals offer analyses of practical applications in cleanroom environments and elaborate on the integration of advanced systems, including our G‑CON POD solutions.
Training Programs and Interactive Learning
Enhance your team’s expertise through specialized e-learning platforms. Courses on GMP fundamentals and advanced regulatory frameworks are available alongside webinars and workshops hosted by industry experts. These programs focus on real-time validation techniques, risk mitigation strategies, and the nuances of environmental monitoring.
Expert Consultations and Modular Integration Support
Engage with specialized consultancies that offer custom compliance strategies, system audits, and process optimization tailored for complex manufacturing setups. Our own G‑CON modular cleanroom systems feature integrated compliance support with pre-validated process controls and automated monitoring, ensuring your facility remains agile amidst evolving standards.
By utilizing these diverse sources, your organization can maintain a proactive approach to compliance, adapt quickly to regulatory changes, and optimize operational efficiency without compromising on safety or quality.
Can G‑CON Provide the Cleanroom Solutions You Need?
We design integrated modular cleanroom systems that transform conventional facilities into agile, high‐performance production environments. Our POD systems deploy swiftly and scale seamlessly to meet your stringent regulatory mandates.
Tailored, Compliant Architectures
Our designs incorporate intelligent control systems featuring automated BMS and EMS integration. Each cleanroom unit undergoes rigorous testing for ISO14644 air quality, GMP compliance, and FDA21CFR11 standards. Key features include:
- Integrated Monitoring: Advanced sensors continuously track particulate levels and airflow, maintaining precise environmental control.
- Flexible Configurations: Whether standard PODs or high‐bay megaPOD systems, our solutions adapt swiftly to your manufacturing needs.
- Predictive Analytics: Embedded management systems forecast operational shifts, enabling proactive adjustments to minimize downtime.
Proven Advantages and Expert Execution
Our extensive portfolio, validated by successful case studies and client testimonials, demonstrates how our systems reduce deployment timelines and enhance process efficiency. Our experienced team tailors each solution to ensure your facility consistently meets evolving industry benchmarks while reducing operational risks.
Our approach unites precision engineering with forward‐looking digital integration. By merging real‑time environmental monitoring and adaptive automation, we equip your facility with the tools to excel under dynamic regulatory conditions. With our modular cleanroom systems, your organization secures unmatched adaptability, operational reliability, and lasting performance.
Contact G‑CON Today
Experience the transformative impact of our modular cleanroom solutions. Our advanced G‑CON systems deliver uncompromising compliance, real‑time environmental control, and adaptive automation designed to optimize your manufacturing performance.
Reasons to Connect
Our cleanroom systems combine stringent ISO14644 standards with GMP‐compliant design and integrated BMS/EMS technology. From standard POD configurations to high‐bay megaPOD systems, every solution is pre‑validated and customized to meet evolving regulatory demands. Continuous sensor analytics and HEPA filtration ensure a stable, contamination‐free atmosphere, safeguarding your product integrity and operational efficiency.
The G‑CON Advantage
- Custom Integration: Rapid deployment and seamless fit into your existing facility.
- Precise Environmental Control: Advanced monitoring systems maintain consistent air quality and aseptic conditions.
- Scalable Efficiency: Prefabricated solutions that reduce downtime and accelerate production timelines.
Reach Out Today
Initiate a personalized consultation to address your facility’s unique requirements and drive sustainable growth through regulatory excellence and operational resilience.
What Are GMP Cleanroom Standards and Why Do They Matter?
GMP Cleanroom Standards establish the technical and procedural framework needed for maintaining aseptic manufacturing environments. Our modular cleanrooms comply with globally recognized criteria, ensuring rigorous contaminant management and precise environmental control through integrated quality management systems.
Critical Components and Their Impact
- Definition and Scope GMP standards set quantitative limits for particulate concentration and detail necessary airflow controls that secure safe production. These parameters are defined in industry benchmarks such as ISO14644.
- Compliance and Quality Assurance Robust testing methods, including continuous ISO14644 particle assessments, verify that processes meet stringent regulatory mandates. Automated data analytics and recursive calibration protocols ensure that every cleanroom dynamically adheres to evolving requirements, thereby minimizing the risk of contamination and non‑compliance.
Strategic Advantages for Your Facility
Our intelligent cleanroom designs incorporate advanced sensor technology and configurations that expedite certification and adapt quickly to regulatory shifts. By continuously monitoring environmental conditions and automating corrective adjustments, our solutions maintain exceptional precision and process consistency. This proactive approach transforms compliance challenges into distinct competitive strengths that enhance production reliability and support scalable manufacturing practices.
Adopting these standards is not merely about meeting regulations—it is a commitment to manufacturing excellence. The synergy of continuous quality assurance, adaptive automation, and integrated digital validation empowers your facility to perform with unmatched efficiency while remaining poised for future industry developments.
How Do GMP Cleanroom Standards Enhance Product Quality?
Our modular cleanrooms exemplify strict adherence to GMP standards, securing and elevating product quality across every production cycle. At G‑CON, we combine advanced automation with rigorous quality control to ensure consistent process integrity.
Enhancing Consistency and Safety
Our systems integrate cutting-edge environmental management with real‑time sensor networks that continuously monitor particulate levels. By employing ISO14644-guided particle assessments alongside automated BMS and EMS controls, our cleanrooms maintain a sterile production environment that minimizes contamination and stabilizes operating conditions. This direct monitoring and adjustment guarantee uniform quality across all production cycles.
Quality Assurance in Action
- Active Environmental Regulation: Automated controls dynamically adjust airflow, temperature, and humidity.
- Comprehensive Testing: Ongoing data logging and strict audits confirm that all parameters meet FDA21CFR11 and GMP requirements.
- Proactive Calibration: A recursive self‑improvement framework utilizes historical performance data to recalibrate operations ahead of potential deviations.
Mitigating Risk and Driving Reliability
G‑CON systems feature advanced HEPA filtration and precise factory acceptance testing. Subtle changes in contaminant levels are detected instantly, prompting automated corrections that transform potential issues into controlled process adjustments. By embedding these stringent quality checks within a scalable, modular design, we enable your facility to maintain high standards while adapting swiftly to evolving regulatory demands.
Incorporating these detailed measures not only ensures compliance but also transforms quality challenges into strategic strengths, supporting sustainable improvements in production reliability.
What Are the Essential Elements of GMP Cleanroom Standards?
G‑CON’s modular cleanroom systems are meticulously engineered to meet global GMP benchmarks through the seamless integration of advanced technologies and rigorous operational protocols.
Assured Quality Through Robust Management
We employ a comprehensive quality management framework that actively controls and verifies every production parameter. Our advanced control algorithms and automated audit trails confirm conformity with FDA21CFR11 and ISO14644 standards, ensuring that every process meets exacting criteria.
State‑of‑the‑Art Environmental Monitoring
Real‑time sensor networks provide continuous feedback on particulate levels, airflow dynamics, and pressure differentials. Smart, calibrated sensors record and process data instantly, enabling our systems to maintain strict aseptic conditions crucial for minimizing micro-contamination.
Proactive Personnel Protocols
Designed with precision, our cleanroom systems incorporate rigorous training and hygiene protocols. Detailed modules reinforce correct gowning practices, aseptic techniques, and contamination control. Regular skills assessments ensure that every team member upholds the highest standards of operational readiness.
Integrated Documentation and Automated Record‑Keeping
Our systems generate digital records that capture environmental data, process adjustments, and audit logs in real time. These secure documentation practices not only guarantee data integrity but also streamline internal reviews and external inspections.
By unifying these technical components—robust quality controls, dynamic environmental monitoring, disciplined personnel protocols, and automated documentation—our integrated approach transforms complex regulatory demands into clear operational advantages. This synergy empowers your facility with the agility and precision required to excel in a rapidly evolving production landscape.
Why Should You Regularly Update Your Cleanroom Standards?
Updating your cleanroom protocols is more than a routine task—it is a strategic necessity that redefines your facility’s operational excellence. Our G‑CON modular cleanrooms integrate cutting-edge sensor networks and adaptive automation to continuously adjust environmental parameters, ensuring that your systems remain aligned with the most current industry frameworks.
Key Revision Triggers
- Environmental Monitoring Shifts: Subtle changes in particle counts or airflow dynamics indicate that your instrumentation now captures new variables.
- Technological Advancements: Breakthroughs in sensor precision and data analytics expose process inefficiencies; integrating these innovations now can optimize performance immediately.
- Regulatory Developments: Updates to ISO14644, FDA21CFR11, and GMP criteria require that your procedures exceed evolving compliance thresholds, thereby reducing audit vulnerabilities.
- Operational Feedback: Consistent audit results and internal assessments provide clear signals for recalibration, ensuring tighter process validation and improved control.
Strategic Advantages
Regular revisions transform reactive upkeep into a proactive, data-driven strategy. By updating your cleanroom standards, you minimize contamination risks, optimize environmental conditions, and establish a framework that anticipates regulatory changes. This iterative approach enhances safety, boosts operational efficiency, and positions your facility to capitalize on emerging technologies. The result is a resilient manufacturing environment that evolves with industry demands and sustains a competitive advantage.
Where Can You Access Trusted GMP Compliance Resources?
Your journey toward operational excellence begins with access to authoritative sources that provide precise, continuously updated GMP insights. At G‑CON, our modular cleanroom solutions are built with integrated compliance intelligence to support your regulatory navigation.
Essential Channels for Compliance Intelligence
Official regulatory websites offer comprehensive guidelines and inspection protocols. Agencies such as the FDA and EMA supply detailed protocols, amendment updates, and inspection criteria that form the cornerstone of true regulatory insight.
Industry associations and reputable publications—such as those from ISPE and ICH—provide rigorously reviewed white papers, compliance benchmarks, and case studies that frame real-world implementation of GMP standards. Their detailed analyses help you understand the nuances of regulatory adherence and quality management.
Numerous online training platforms offer certification courses and workshops focused on GMP standards. These programs equip your team with practical expertise and robust methodologies for maintaining compliance. Specialized consultancies, skilled in integrating systems like our BMS and EMS interfaces, deliver tailored strategies that transform regulatory complexities into operational strengths.
Reliable resources consistently supply current technical data, in-depth analysis, and real-world examples of successful compliance. By incorporating these channels into your compliance framework, you establish an ecosystem that supports continuous improvement, enhances process stability, and strengthens your competitive position.
How Can G‑CON Provide the Cleanroom Solutions You Need?
G‑CON transforms traditional facilities by delivering flexible, fully integrated modular environments that meet stringent regulatory demands while boosting operational performance. Our systems are meticulously engineered to provide your organization with uncompromised compliance and efficiency.
Tailored Modular Solutions
Our portfolio spans from standardPOD units to expansive high‑bay megaPOD systems, designed to adapt to your unique manufacturing challenges. Each system incorporates Building and Environmental Management Systems(EMS is optional) that:
- Monitor air quality in real time using precise sensor networks.
- Maintain sterile conditions through automated environmental controls.
- Conform to ISO14644, GMP, and FDA21CFR11 regulations.
Proven Economic and Operational Advantages
Experience benefits that directly impact your production cycle:
- Streamlined Installation: Prefabricated, offsite construction and plug‑and‑play designs dramatically shorten build times, moving your facility rapidly from planning to production.
- Enhanced Compliance: Advanced controls and continuous data logging ensure each unit consistently meets rigorous quality and safety standards, minimizing audit risks.
- Scalable Innovation: Our modular designs grow alongside your operations, accommodating diverse requirements from biopharmaceutical production to semiconductor fabrication without sacrificing reliability.
Customer-Centric Excellence
Our commitment to precision engineering and adaptive innovation is reflected in extensive client case studies. When you deploy G‑CON solutions, you gain:
- A robust framework that anticipates regulatory shifts and adapts to emerging technologies.
- Predictive analytics and dynamic monitoring that preempt potential operational issues.
- Comprehensive support throughout your project—from initial design consulting to on‑site deployment, ensuring every detail is aligned with your objectives.