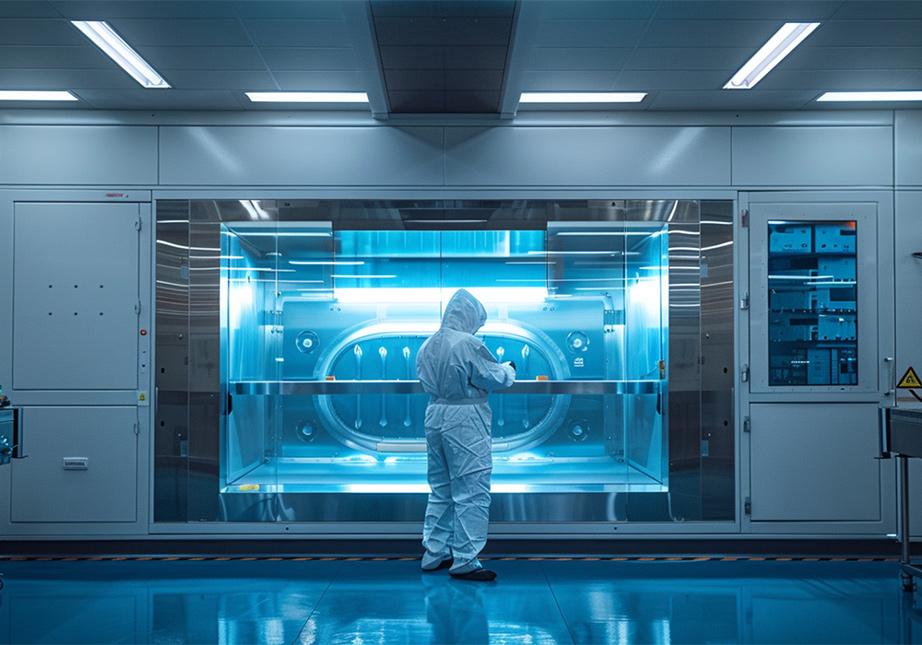
Jun 02, 2024
Aerospace Cleanrooms
Understanding Aerospace Cleanrooms: An Overview
Aerospace cleanrooms are precision-engineered environments crucial for the manufacturing and research of aerospace components. Unlike cleanrooms in other industries, aerospace cleanrooms are designed with specific functionalities to handle the intricate and sensitive nature of aerospace applications.
Key Components and Systems
The core of an aerospace cleanroom lies in its ability to maintain a contamination-free environment. This is achieved through:
- Controlled Air Quality: Utilizing High-Efficiency Particulate Air (HEPA) and Ultra-Low Particulate Air (ULPA) filtration systems to remove contaminants from the air.
- Regulated Environmental Conditions: Ensuring optimal temperature, humidity, and pressure levels are consistently maintained.
- Specialized Equipment: Employing state-of-the-art technology and materials, such as modular and softwall cleanrooms, to support the unique requirements of aerospace manufacturing.
Contribution to Aerospace Safety and Reliability
Aerospace cleanrooms are integral to the safety and reliability of aerospace missions. They ensure:
- Component Integrity: By eliminating particulate contamination, cleanrooms prevent defects in sensitive aerospace components, such as optical devices and electronic systems.
- Mission Success: The reliability of aerospace missions hinges on the flawless performance of each component, which is largely attributed to the stringent manufacturing conditions provided by aerospace cleanrooms.
At G-Con, we understand the pivotal role these environments play. Our tailored cleanroom solutions, including prefabricated POD cleanrooms, are designed to meet the rigorous standards required for aerospace applications, ensuring that your mission-critical projects are supported by the highest quality controlled environments.
Standards and Classifications: Navigating Through ISO and ASTM
Aerospace cleanrooms are governed by stringent standards that dictate their design, construction, and operation. The ISO 14644-1 and Federal Standard 209E are pivotal in defining the level of air purity by specifying the maximum allowable particulate concentration. These standards are critical as they ensure the reliability and safety of aerospace components which are sensitive to contamination.
ISO and ASTM Standards in Aerospace Cleanrooms
- ISO 14644-1: This standard provides the classification of air cleanliness levels based on the concentration of airborne particles. For aerospace applications, adherence to this standard is non-negotiable as it directly impacts the integrity of the manufacturing process.
- ASTM Standards: These standards cover a range of materials and processes, including the testing and quality assurance of the cleanroom environment.
Impact on Design and Operation
Compliance with these standards influences every aspect of a cleanroom, from the airflow systems to the materials used in construction. They ensure that the environment is precisely controlled to prevent contamination that could compromise aerospace components.
Consequences of Non-Compliance
For aerospace manufacturers, failing to meet these standards can lead to catastrophic failures in aerospace missions. Non-compliance not only risks the functionality of aerospace components but also the safety of entire missions.
Ensuring Ongoing Compliance
To maintain compliance, aerospace cleanroom operators must engage in continuous monitoring and adhere to a strict maintenance schedule. Regular audits and updates to procedures in response to evolving standards are essential to uphold the integrity of the cleanroom environment.
By understanding and implementing these standards, you ensure the optimal performance of aerospace cleanrooms and the success of aerospace missions. At G-Con, we prioritize compliance with these standards in all our cleanroom solutions, ensuring that your operations meet the highest levels of cleanliness and control.
Designing Aerospace Cleanrooms: Principles and Practices
Foundational Design Principles
When constructing an aerospace cleanroom, the foundational design principles revolve around creating a controlled environment that minimizes particulate contamination. This is achieved through:
- Controlled Airflow: Establishing unidirectional or laminar airflow to remove contaminants efficiently.
- Pressurization: Maintaining positive pressure to prevent infiltration of pollutants.
- Material Selection: Utilizing non-particulating, non-outgassing materials resistant to sterilization processes.
Impact of Materials and Technologies
The choice of materials and technologies is pivotal in determining the efficiency and functionality of aerospace cleanrooms. For instance:
- Advanced Filtration: HEPA and ULPA filters are essential for trapping minuscule contaminants that could jeopardize aerospace component integrity.
- Smart Monitoring Systems: These ensure real-time tracking of environmental conditions, allowing for immediate adjustments to maintain standards.
Role of Modular Cleanroom Design
Modular cleanroom design, such as our G-Con PODs, offers versatility and scalability in aerospace applications. Benefits include:
- Rapid Deployment: Prefabricated units allow for quicker installation compared to traditional construction.
- Customization: Configurations can be tailored to specific aerospace manufacturing processes.
- Factory Acceptance Testing: Ensures compliance with standards before on-site assembly.
Design Considerations for Aerospace Manufacturing
Design considerations for aerospace cleanrooms must align with the specific manufacturing processes they support. This includes:
- Space Utilization: Optimizing layout for equipment and personnel flow.
- Material Handling: Incorporating features like air showers and pass-through chambers to reduce contamination risks.
- Environmental Control: Tailoring temperature, humidity, and ventilation settings to the requirements of aerospace component manufacturing.
At G-Con, we understand these nuances and work with you to ensure your aerospace cleanroom is designed for peak performance and compliance.
Air Filtration and Environmental Control Systems
Essential Air Filtration Systems
In aerospace cleanrooms, air filtration systems are paramount to maintaining the required cleanliness levels. The systems typically include:
- HEPA/ULPA Filters: High-Efficiency Particulate Air (HEPA) and Ultra-Low Particulate Air (ULPA) filters are crucial for trapping particles as small as 0.1 to 0.3 microns.
- Laminar Flow Systems: These create a uniform flow of air that captures and directs particles out of the cleanroom, essential for maintaining ISO class standards.
Managing Environmental Conditions
Environmental control systems in aerospace cleanrooms manage critical conditions, including:
- Temperature: Typically maintained between 67-77F for ISO Class 5-8 cleanrooms.
- Humidity: Kept at 30-50% to prevent static build-up and microbial growth.
- Pressure: Positive pressure is maintained to prevent ingress of contaminants.
Overcoming Implementation Challenges
Challenges in implementing these systems can include:
- Complex Integration: Ensuring all systems work in harmony without compromising the cleanroom’s integrity.
- Sustainability: Balancing energy efficiency with the need for constant filtration and climate control.
Impact on Cleanroom Operations
The efficiency of air filtration and environmental control systems has a direct impact on:
- Operational Costs: More efficient systems can reduce energy consumption and operational expenses.
- Compliance: Effective systems ensure ongoing adherence to regulatory standards, which is critical for your operations.
At G-Con, we provide solutions that address these challenges, ensuring your aerospace cleanroom operates at peak efficiency and compliance.
Contamination Control Strategies
Controlling contamination is a critical aspect of maintaining aerospace cleanroom standards. Understanding common contamination sources and implementing rigorous control measures are essential for the integrity of aerospace components.
Mitigating Common Contamination Sources
Contamination can originate from several sources within aerospace cleanrooms:
- Personnel: Human activity is a significant contributor, with skin flakes, cosmetics, and even breath posing risks.
- Materials: Particulates from degrading materials or improper handling can contaminate the environment.
- Equipment: Machinery can release particles or harbor contaminants if not properly maintained.
To mitigate these risks, our cleanrooms are designed with:
- Air Showers: To remove particulates from personnel and materials entering the cleanroom.
- Pass-Through Chambers: For safely transferring materials without exposing the cleanroom to outside air.
Personnel Hygiene and Behavior Protocols
Personnel are required to follow strict hygiene and behavior protocols, including:
- Gowning Procedures: Donning specialized apparel designed to trap contaminants.
- Behavioral Training: Educating staff on movements and actions that minimize particulate generation.
Cleaning and Maintenance Procedures
Regular cleaning and maintenance are non-negotiable for aerospace cleanroom standards:
- Scheduled Cleanings: Using cleanroom-specific products and procedures to maintain cleanliness.
- Preventive Maintenance: Regular checks and servicing of equipment to prevent contamination.
Monitoring and Detection Systems
Early identification of contamination is facilitated by:
- Environmental Monitoring Systems: Continuously assessing particle counts and environmental conditions.
- Smart Sensors: Alerting staff to deviations, enabling prompt corrective actions.
At G-Con, we understand the importance of these strategies and provide the necessary equipment and expertise to ensure your aerospace cleanroom meets the highest standards of contamination control.
Equipment and Supplies for Aerospace Cleanrooms
Aerospace cleanrooms require specialized equipment and supplies to maintain the stringent cleanliness standards necessary for aerospace component manufacturing. Understanding the critical role of each element helps ensure the integrity of the cleanroom environment.
Selecting Cleanroom-Compliant Materials
Procurement managers play a vital role in selecting the right materials and equipment. The selection process involves:
- Compatibility: Ensuring materials are compatible with the cleanroom’s ISO class and the specific aerospace application.
- Quality: Choosing supplies that meet industry standards for durability and performance.
- Supplier Reputation: Working with reputable suppliers known for their commitment to cleanroom standards.
Role of HEPA Filters and Cleanroom Garments
- HEPA Filters: These are essential for trapping particles that could compromise the manufacturing process, maintaining the air purity required for aerospace applications.
- Cleanroom Garments: Specialized apparel is designed to minimize human-borne contamination, a critical consideration for maintaining cleanroom integrity.
G-Con’s Support with Modular Solutions
At G-Con, we support aerospace cleanrooms by providing:
- Modular Cleanroom Solutions: Our prefabricated PODs offer flexibility and scalability, essential for the dynamic needs of aerospace cleanrooms.
- Compliant Supplies: We ensure that all our supplies, from filtration systems to garments, meet the rigorous standards required for aerospace applications.
Our commitment is to provide you with comprehensive solutions that meet your aerospace cleanroom needs, ensuring that your operations are efficient, compliant, and successful.
Training and Compliance for Cleanroom Personnel
Essential Training Programs for Aerospace Cleanroom Technicians
At G-Con, we recognize that the proficiency of cleanroom technicians is vital for the success of aerospace cleanrooms. Training programs are meticulously designed to cover:
- Cleanroom Protocols: Comprehensive understanding of standard operating procedures and best practices.
- Contamination Control: Techniques to minimize contamination risks, including proper gowning and hygiene practices.
- Equipment Handling: Correct usage and maintenance of cleanroom-specific equipment to prevent contamination.
Addressing Aerospace Manufacturing Requirements
Our training programs are tailored to meet the unique demands of aerospace manufacturing, focusing on:
- Precision and Detail: Emphasizing the importance of attention to detail in an industry where even the smallest particle can lead to failure.
- Regulatory Standards: Ensuring technicians are well-versed in relevant ISO and ASTM standards for aerospace cleanrooms.
Compliance and Certification Processes
To work in aerospace cleanrooms, personnel must undergo:
- Certification: Achieving recognized qualifications that validate their knowledge and adherence to cleanroom standards.
- Regular Assessments: Demonstrating ongoing compliance with industry regulations through periodic evaluations.
Adapting to New Standards and Technologies
We advocate for continuous education to keep pace with:
- Evolving Standards: Updating training materials to reflect the latest industry standards and practices.
- Technological Advancements: Incorporating new technologies and procedures into the curriculum to maintain cutting-edge expertise.
Our commitment is to ensure that you and your team are equipped with the knowledge and skills necessary to maintain the highest standards of aerospace cleanroom operations.
Cost Management and Budgeting for Aerospace Cleanrooms
Understanding the financial aspects of aerospace cleanrooms is crucial for effective budgeting and cost management. Initial setup costs can be substantial, encompassing design, construction, equipment, and technology. Operational expenses include maintenance, monitoring, and personnel training.
Initial Setup and Operational Costs
- Design and Construction: The complexity of aerospace cleanroom design often necessitates a higher initial investment.
- Equipment and Technology: Advanced filtration systems and environmental controls are essential but come with significant costs.
Effective Budgeting Strategies
To manage these costs effectively, aerospace cleanroom operators should:
- Detailed Planning: Forecast all potential expenses to avoid unexpected costs.
- Investment in Quality: Opt for high-quality materials and equipment that, while initially more expensive, reduce long-term maintenance costs.
Implementing Cost-Saving Measures
Cost-saving measures that do not compromise standards include:
- Energy-Efficient Systems: Investing in energy-efficient HVAC and lighting systems to reduce utility costs.
- Preventive Maintenance: Regular maintenance can prevent costly repairs and downtime.
Modular Cleanroom Design as a Cost-Effective Solution
Our G-Con modular cleanroom design offers:
- Scalability: Adapt the cleanroom size to your current needs, with the option to expand as necessary.
- Reduced Construction Time: Prefabricated components shorten the construction timeline, reducing labor costs.
- Customization: Tailor the cleanroom to your specific requirements without the expense of traditional construction.
By partnering with G-Con, you can achieve a balance between cost efficiency and compliance with aerospace cleanroom standards.
Technological Advancements and Innovations in Aerospace Cleanrooms
The landscape of aerospace cleanrooms is continually evolving, driven by technological advancements that enhance their design and operation. As a leader in cleanroom solutions, G-Con stays at the forefront of these innovations, ensuring that our services support your need for efficiency, safety, and compliance.
Impact of Recent Technological Advancements
Recent innovations have significantly influenced aerospace cleanrooms:
- Smart Monitoring Systems: These systems provide real-time data on environmental conditions, allowing for immediate adjustments to maintain the required standards.
- Advanced Materials and Coatings: New materials reduce particle shedding and resist microbial growth, contributing to a cleaner environment.
- Robotics and Automation: Automation of standard upkeep tasks reduces human intervention and potential contamination.
Contributions to Efficiency, Safety, and Compliance
These technological advancements contribute to:
- Enhanced Efficiency: Automated systems streamline operations, reducing the time and labor required for maintenance.
- Increased Safety: Real-time monitoring and advanced materials minimize the risk of contamination, ensuring the safety of aerospace components.
- Improved Compliance: Smart systems facilitate adherence to regulatory standards by providing precise control over cleanroom conditions.
Emerging Trends Shaping Aerospace Manufacturing
Emerging trends include:
- AI for Predictive Maintenance: Leveraging artificial intelligence to predict and prevent equipment failures before they occur.
- Nanotechnology: Utilizing nanomaterials for superior filtration and contamination control.
- Sustainable Operations: Innovations aimed at reducing the environmental impact of cleanroom operations.
Staying Ahead of Technological Advancements
To maintain a competitive edge, aerospace cleanroom operators should:
- Continuous Learning: Stay informed about the latest developments in cleanroom technology.
- Strategic Partnerships: Collaborate with industry leaders like G-Con for access to cutting-edge cleanroom solutions.
- Investment in Innovation: Allocate resources to adopt and integrate new technologies into cleanroom operations.
By partnering with G-Con, you can ensure that your aerospace cleanroom is equipped with the latest advancements, keeping you ahead in a rapidly advancing industry.
Challenges and Solutions in Aerospace Cleanroom Operation
Operating aerospace cleanrooms presents unique challenges that require precise solutions to maintain the integrity of sensitive aerospace components.
Addressing Operational Challenges
Aerospace cleanrooms face several operational challenges:
- Contamination Control: The paramount challenge is preventing contamination that can compromise aerospace components.
- Adapting to Evolving Standards: Cleanrooms must stay compliant with changing industry standards, such as ISO 14644-1 and Federal Standard 209E.
- Energy Efficiency: Balancing the high energy demands of maintaining controlled environments with the need for sustainable operations.
To address these challenges, we implement:
- Rigorous Cleaning Protocols: Utilizing professional cleaning services and cleanroom-specific products.
- Continuous Monitoring: Employing smart monitoring systems for real-time environmental control.
- Sustainable Practices: Integrating energy-efficient technologies and practices into cleanroom design.
Role of Modular Cleanroom Solutions
Modular cleanroom solutions, like our G-Con PODs, offer:
- Flexibility: Easily reconfigured layouts to adapt to changing processes or standards.
- Scalability: The ability to scale operations up or down without extensive renovations.
- Efficiency: Reduced construction time and potential for lower operational costs.
Leveraging Expertise for Optimization
At G-Con, we leverage our expertise to optimize your cleanroom operations by:
- Custom Design: Tailoring cleanroom designs to meet specific aerospace manufacturing needs.
- Advanced Technologies: Incorporating the latest in filtration and environmental control systems.
- Expert Consultation: Providing access to our knowledgeable team for ongoing support and guidance.
Our commitment is to provide solutions that not only meet but exceed the operational demands of aerospace cleanrooms, ensuring your projects are carried out with the highest standards of quality and safety.
The Role of Aerospace Cleanrooms in Mission Success
Aerospace cleanrooms are integral to the success of aerospace missions, providing the precision-engineered environments necessary for the development and assembly of aerospace components. The controlled conditions within these cleanrooms directly contribute to the reliability and performance of aerospace systems.
Ensuring Reliability of Aerospace Missions
- Contamination Elimination: By meticulously controlling particulate levels, aerospace cleanrooms prevent contamination that could lead to component failures.
- Controlled Conditions: The stringent environmental controls within cleanrooms ensure that components are manufactured and tested under consistent conditions, vital for the success of aerospace missions.
Implications of Cleanroom Failures
- Mission Compromise: Any failure in maintaining cleanroom standards can result in compromised aerospace components, potentially leading to mission failure.
- Safety Risks: The high standards of aerospace cleanrooms are not just about mission success but also about ensuring the safety of astronauts and the integrity of space exploration missions.
Integrity and Performance Assurance
- Performance Standards: Aerospace cleanrooms are designed to meet specific ISO classes, ensuring that components are free from defects that could affect performance.
- Quality Control: Rigorous testing and quality assurance practices within cleanrooms are essential for the validation of aerospace components.
Advancing Aerospace Technology
- Innovation Support: Cleanrooms provide the environment necessary for research and development of new aerospace technologies.
- Technological Advancement: The precision and control offered by aerospace cleanrooms facilitate the advancement of aerospace engineering and design.
At G-Con, we understand the critical role that aerospace cleanrooms play in mission success. Our modular cleanroom solutions are designed to support your aerospace projects, ensuring that every component meets the highest standards of quality and performance.
Partner with G-Con for Your Aerospace Cleanroom Solutions
At G-Con, we understand the critical importance of precision-engineered cleanroom environments in the aerospace industry. Our expertise in designing, implementing, and maintaining cleanroom solutions ensures that your operations meet the stringent standards required for aerospace applications.
Modular Cleanroom Options for Aerospace Applications
G-Con offers a range of modular cleanroom options tailored to the aerospace sector:
- standardPOD: A versatile solution for various aerospace cleanroom needs.
- mobilisPOD: For operations requiring mobility within the facility.
- megaPOD: Designed for large-scale aerospace projects.
- POD System: A comprehensive cleanroom system with integrated components.
- smartPOD: Incorporates advanced automation and controls for optimal operation.
Ensuring Compliance with Aerospace Cleanroom Standards
Partnering with G-Con provides you with the assurance of compliance:
- Regulatory Adherence: Our cleanrooms are designed to meet ISO 14644-1, Federal Standard 209E, and other relevant standards.
- Factory Acceptance Testing: All our cleanrooms undergo rigorous testing to ensure they meet the required specifications before delivery.
Why Choose G-Con?
Choosing G-Con for your aerospace cleanroom needs offers several advantages:
- Expertise: Our team’s extensive knowledge ensures that your cleanroom is designed and built to the highest standards.
- Customization: We provide tailored solutions that fit your specific aerospace application requirements.
- Support: G-Con is committed to offering exceptional support throughout the design, installation, and maintenance of your cleanroom.
For aerospace cleanroom solutions that combine quality, integrity, and compliance, reach out to us at G-Con. We are dedicated to supporting the success of your aerospace missions.