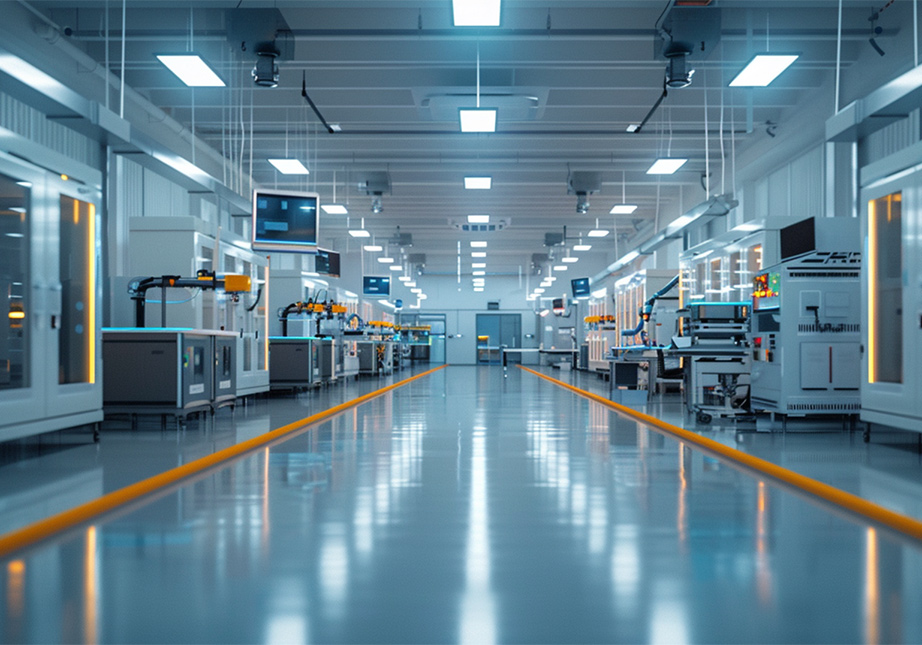
Jun 03, 2024
Electronics Cleanrooms
Understanding Electronics Cleanrooms: An Overview
Electronics cleanrooms are specialized environments meticulously designed to minimize the presence of airborne particles and control environmental parameters such as temperature, humidity, and pressure. The primary purpose of these precision-controlled spaces is to protect sensitive electronic components during manufacturing, ensuring their reliability and quality.
Core Requirements for Electronics Cleanrooms
To establish an electronics cleanroom, several fundamental requirements must be met:
- Contamination Control: The cornerstone of cleanroom functionality is the rigorous control of contamination. This encompasses the implementation of strict protocols to manage particulate matter, out-gassing, and static electricity.
- Air Quality Management: Cleanrooms must maintain specific air quality levels, typically regulated by ISO 14644 standards, which dictate the maximum allowable particle concentration.
- Environmental Stability: Temperature and humidity are precisely regulated to prevent material degradation and ensure process consistency.
- Electrostatic Discharge (ESD) Management: ESD-sensitive environments require materials and practices that mitigate the risk of electrostatic discharge, which can damage electronic components.
Ensuring Reliability and Quality
At G-Con, our cleanroom solutions are designed to address these requirements effectively. We ensure:
- Optimized Airflow: Our cleanrooms are engineered with airflow optimization to remove contaminants efficiently and maintain a stable environment conducive to high-precision manufacturing.
- Advanced Filtration: We incorporate HEPA/ULPA filtration systems to capture even the smallest particles, ensuring the highest air purity levels.
- Customized Design: Recognizing the unique needs of each client, we offer tailored designs, from softwall to rigid wall cleanrooms, that align with your specific manufacturing processes.
By adhering to these principles, we help you establish a cleanroom that underpins the integrity and success of your electronics manufacturing operations.
ISO Classifications and Their Importance in Cleanroom Design
Understanding the ISO classifications relevant to electronics cleanrooms is essential for ensuring the integrity of sensitive electronic components. ISO 14644-1 is the cornerstone standard that specifies the cleanliness levels of air in cleanrooms and associated controlled environments. The classification of a cleanroom is determined based on the concentration of airborne particles, which is critical for preventing contamination during the manufacturing process.
Impact on Cleanroom Design and Operation
The ISO classifications directly influence the architectural and operational aspects of cleanroom design. For instance, an ISO 5 cleanroom permits fewer airborne particles than an ISO 8 environment, necessitating more stringent air filtration systems and controls. This classification system ensures that the design of the cleanroom, including its HVAC, filtration, and airflow patterns, aligns with the required cleanliness level for electronic manufacturing processes.
Criticality of Adherence to ISO Standards
Adherence to ISO standards is non-negotiable in electronics manufacturing due to the high sensitivity of electronic components to contaminants. Compliance with these standards not only ensures product quality but also minimizes the risk of costly production errors and rework. Our commitment at G-Con to these standards reflects in our cleanroom solutions, ensuring that your operations meet global regulatory requirements.
Guiding Maintenance Protocols
ISO classifications provide a framework for establishing maintenance protocols. Regular testing and certification are necessary to ensure that cleanrooms continue to meet the designated ISO class. This includes routine monitoring of particulate levels, filter integrity checks, and adherence to cleaning procedures, all of which are critical for maintaining the controlled environment necessary for electronics manufacturing.
Architectural and Engineering Considerations for Cleanroom Design
When designing an electronics cleanroom, architectural and engineering considerations are paramount. The layout must facilitate a contamination-controlled environment, which is achieved through precise engineering of airflow, pressure, temperature, and humidity. The materials used in construction must be non-particulating and easy to clean, ensuring that they do not contribute to contamination.
Airflow, Filtration, and Static Control in Cleanrooms
Airflow patterns are engineered to sweep particles away from critical processing areas and are typically unidirectional or laminar flow. Filtration systems, including HEPA and ULPA filters, are essential for trapping contaminants. Effective static control is achieved through the use of ESD materials and equipment, preventing electrostatic discharge which can damage sensitive electronic components.
The Role of Modular Cleanroom Design
Modular cleanroom design, such as our G-Con PODs, offers flexibility and scalability in the electronics industry. These prefabricated units can be customized to meet specific ISO classifications and are Factory Acceptance Tested to ensure compliance before deployment.
Optimizing Cleanroom Design for Efficiency and Compliance
Optimizing cleanroom design involves a balance between operational efficiency and adherence to standards. This includes selecting the right materials for construction, implementing smart automation for environmental monitoring, and ensuring that the design accommodates future technological advancements or changes in production needs. At G-Con, we ensure that our cleanroom solutions are designed to meet your specific requirements while maintaining compliance with industry standards.
Controlling Contamination: Strategies and Best Practices
Contamination control is the linchpin of electronics cleanroom operations. The primary sources of contamination include particulate matter from the air, out-gassing from materials within the cleanroom, and human-borne contaminants.
Minimizing Contamination Risks
To minimize contamination risks, cleanroom personnel must adhere to strict protocols. This includes proper gowning procedures before entering the cleanroom and adhering to behavioral guidelines that reduce particulate generation. Our training programs at G-Con ensure that your staff is well-versed in these critical procedures.
Protocols for Material and Equipment Handling
Material and equipment handling protocols are established to prevent the introduction of contaminants. This involves using antistatic packaging to transport components and implementing clean storage solutions to maintain the integrity of materials when not in use.
Regular Monitoring and Maintenance
Regular monitoring and maintenance are essential for sustaining contamination control. This includes scheduled cleanroom cleaning and maintenance, as well as real-time monitoring of particulate levels. At G-Con, we provide comprehensive maintenance services to ensure that your cleanroom continues to meet the required ISO standards and operates at peak efficiency.
Selecting the Right Equipment and Materials for Cleanrooms
When outfitting an electronics cleanroom, the selection of equipment and materials is governed by stringent criteria to maintain the integrity of the controlled environment. At G-Con, we understand that every detail matters in ensuring the optimal performance of your cleanroom.
Criteria for Cleanroom Equipment Selection
The equipment chosen for a cleanroom must meet specific standards to prevent contamination:
- HEPA/ULPA Filtration: High-Efficiency Particulate Air (HEPA) or Ultra-Low Particulate Air (ULPA) filters are essential for trapping airborne particles.
- Antistatic Surfaces: Surfaces must be designed to prevent electrostatic discharge, which can damage sensitive electronic components.
- Controlled Pressure Systems: Equipment must maintain the required pressure differentials to prevent cross-contamination.
- High Purity Piping: Piping systems should be made of materials that do not shed particles or harbor microbial growth.
Impact of Materials on Contamination Levels
Materials used within cleanrooms directly affect contamination levels:
- Non-Particulating Materials: Surfaces and construction materials must not release particles into the cleanroom environment.
- Compatibility with Cleaning Agents: Materials must withstand regular cleaning with approved disinfectants without degrading.
Importance of Cleanroom-Specific Furniture and Fixtures
Furniture and fixtures must be designed for cleanrooms to ensure they do not contribute to contamination. This includes:
- Seamless and Non-Porous Surfaces: To facilitate easy cleaning and disinfection.
- Minimal Design: To reduce areas where contaminants can accumulate.
Personal Protective Equipment (PPE) Considerations
Selecting PPE for cleanroom staff involves:
- Material Suitability: Fabrics that provide a barrier against contaminants while allowing for breathability.
- Proper Fit: Ensuring that PPE fits correctly to prevent gaps where contaminants could enter.
- Compliance with Standards: PPE must meet the standards required for the cleanroom’s ISO classification.
By meticulously selecting equipment and materials that meet these criteria, you can maintain the controlled environment necessary for your electronics manufacturing processes.
Implementing Environmental Monitoring and Control Systems
Effective monitoring of environmental conditions is critical in electronics cleanrooms. At G-Con, we integrate advanced technologies to ensure real-time monitoring and control of particulate levels, temperature, and humidity, which are vital to maintaining the stringent standards required for electronics manufacturing.
Technologies for Real-Time Monitoring
Our cleanrooms are equipped with state-of-the-art particle counters and environmental monitoring systems that provide continuous surveillance of particulate levels. These systems are designed to alert you to any deviation from the established parameters, allowing for immediate corrective action.
Contribution of Temperature and Humidity Control
Temperature and humidity control systems are integral to cleanroom operations. They not only ensure the comfort and safety of personnel but also maintain the integrity of sensitive electronic components. By keeping these environmental factors within precise limits, we prevent static build-up and condensation, which could otherwise lead to product defects.
Addressing Challenges in Environmental Conditions
Maintaining optimal environmental conditions can be challenging, but our cleanroom solutions are designed to address these complexities. With automated control systems and regular maintenance protocols, we ensure that the cleanroom environment remains within the required specifications, thus safeguarding your manufacturing processes against contamination risks.
Operational Protocols for Cleanroom Staff and Procedures
Training and Certification for Cleanroom Technicians
At G-Con, we recognize that the expertise of cleanroom technicians is fundamental to the success of your operations. Training for these critical roles encompasses both theoretical and practical aspects of cleanroom standards, contamination control, and specific procedures relevant to electronics manufacturing. Certification, often aligned with ISO standards and industry-specific regulations, validates the technician’s proficiency and commitment to upholding the integrity of the cleanroom environment.
Ensuring Compliance and Safety Through SOPs
Standard Operating Procedures (SOPs) are the backbone of cleanroom compliance and safety. These documented protocols provide clear instructions for every process, from gowning to equipment operation, ensuring consistency and minimizing the risk of contamination. Our SOPs are meticulously developed to align with ISO classifications and are regularly reviewed to incorporate the latest industry best practices.
Best Practices for Cleanroom Attire and Behavior
To prevent contamination, cleanroom attire and behavior must adhere to stringent guidelines. This includes the use of appropriate garments, such as gowns, hoods, and boots, designed to trap particulates. Behavior protocols dictate movement and actions within the cleanroom to reduce the generation of contaminants. We provide comprehensive guidelines to ensure that your staff’s attire and behavior align with the required cleanliness levels.
Role of Ongoing Education and Training Programs
Continuous education and training programs are vital for maintaining operational excellence in cleanroom environments. These programs keep staff updated on the latest cleanroom technologies, contamination control strategies, and regulatory changes. At G-Con, we support your commitment to excellence by offering ongoing education opportunities that enhance the skills and knowledge of your cleanroom personnel.
Advancements in Cleanroom Technology and Materials
The landscape of cleanroom technology is continually evolving, with recent advancements significantly impacting design and operation. At G-Con, we stay at the forefront of these developments to provide you with cutting-edge solutions.
Technological Innovations Impacting Cleanroom Design
Recent technological advancements have introduced:
- SmartPOD Automation: Automation technologies that streamline cleanroom operations, enhancing precision and reducing human error.
- Advanced Filtration Systems: Innovations in HEPA/ULPA filtration technology that offer higher efficiency in particle removal.
- Environmental Monitoring Tools: Sophisticated sensors and control systems for real-time monitoring of cleanroom conditions.
Contributions of Materials Science to Cleanroom Environments
Materials science has played a pivotal role in advancing cleanroom environments:
- Antistatic Surfaces: Development of new materials that effectively manage static electricity, crucial for protecting sensitive electronic components.
- Fire Retardant Materials: Enhanced safety with materials that reduce fire risks, ensuring a safer working environment.
Enhancing Operational Flexibility with Modular Solutions
Our modular cleanroom solutions, such as the standardPOD and megaPOD, offer:
- Scalability: The ability to expand or reconfigure cleanroom spaces as your needs evolve.
- Rapid Deployment: Prefabricated units that can be quickly installed, minimizing downtime.
Future Trends in Electronics Cleanrooms
Looking ahead, we anticipate:
- Sustainability: A growing emphasis on environmental sustainability in cleanroom design and operation.
- Integration with Industry 4.0: Increased use of IoT and AI for enhanced efficiency and predictive maintenance in cleanrooms.
By integrating these advancements, we ensure that your cleanroom is not only compliant with current standards but also ready for the future.
Regulatory Oversight of Electronics Cleanrooms
In the electronics industry, cleanroom standards are overseen by regulatory bodies such as the International Organization for Standardization (ISO) and the Institute of Environmental Sciences and Technology (IEST). These organizations establish the classifications and best practices that dictate the level of cleanliness required for various manufacturing processes.
Impact of Regulations on Cleanroom Design and Operation
Regulations profoundly influence the design, operation, and maintenance of cleanrooms. They determine the air quality, construction materials, and equipment that must be used to achieve the necessary controlled environment. For instance, ISO 14644-1 specifies the maximum allowable particulate concentration in cleanroom air, guiding the selection of air filtration systems.
Challenges in Regulatory Compliance
Achieving and maintaining regulatory compliance can be challenging due to the dynamic nature of standards and the technical complexity of cleanroom operations. Common hurdles include staying abreast of updates to regulations and integrating new technologies that meet stricter controls.
Ensuring Ongoing Compliance
To ensure ongoing compliance, organizations must conduct regular cleanroom certifications and audits. At G-Con, we support you in this endeavor by providing cleanrooms that are Factory Acceptance Tested and designed to meet the latest standards. Our solutions, including the smartPOD, are engineered to adapt to evolving regulations, ensuring that your operations remain compliant now and in the future.
Environmental Sustainability in Cleanroom Operations
Electronics cleanrooms are designed with environmental sustainability in mind. At G-Con, we incorporate advanced cleanroom technology to reduce environmental impact. This includes the use of energy-efficient HVAC systems and LED lighting, which not only lower energy consumption but also decrease the heat load, allowing for more precise temperature control.
Safety Protocols for Cleanroom Workers
Safety is paramount in cleanroom operations. Our safety protocols are comprehensive, encompassing the use of personal protective equipment (PPE), safe handling of materials, and emergency response procedures. We ensure that you and your staff are trained in these protocols to maintain a safe working environment.
Managing and Disposing of Hazardous Materials
Proper management and disposal of hazardous materials are critical components of cleanroom operations. We provide guidance on safe storage, handling, and disposal practices that comply with environmental regulations, ensuring that your operations are not only safe for your workers but also for the environment.
Energy Efficiency in Modern Cleanroom Design
Energy efficiency plays a significant role in the design of modern cleanrooms. Our designs optimize the use of resources, reducing operational costs and environmental footprint. By integrating energy-efficient components and smart control systems, we help you achieve a balance between optimal cleanroom performance and environmental responsibility.
Addressing Operational Challenges in Cleanroom Management
Cleanroom managers often face challenges such as maintaining stringent contamination control, ensuring equipment functionality, and adhering to regulatory compliance. Proactive maintenance strategies are crucial in addressing these challenges.
Proactive Maintenance Strategies
Implementing a proactive maintenance schedule can significantly reduce the risk of downtime. Regularly scheduled inspections and servicing of critical systems, such as HVAC and filtration units, ensure that potential issues are identified and addressed before they escalate into major problems.
Simplifying Maintenance with Modular Systems
Our modular cleanroom systems, including the standardPOD and megaPOD, are designed to simplify maintenance. The prefabricated nature of these units allows for easy access to components for cleaning and servicing, reducing the time and complexity involved in maintenance tasks.
Leveraging Technology for Streamlined Management
Technology plays a pivotal role in streamlining cleanroom management processes. Automation systems, such as our smartPOD automation, can monitor environmental conditions and alert managers to deviations, facilitating timely interventions. Additionally, integrated management software can track maintenance schedules, filter life cycles, and certification deadlines, ensuring that your cleanroom operates within the required parameters.
Tailored Modular Cleanroom Solutions from G-Con
At G-Con, we understand that each electronics manufacturing process has unique requirements. Our modular cleanroom solutions are designed to meet the specific needs of your operations, ensuring that you have a controlled environment tailored to your product specifications.
Customization Options for Operational Excellence
We offer a range of customization options to address the unique challenges of your cleanroom operations. Whether you need specific ISO class ratings, unique airflow patterns, or particular temperature and humidity controls, our design team works with you to create a cleanroom that fits your exact requirements.
Comprehensive Client Support
From the initial design phase to implementation and beyond, G-Con provides end-to-end support. Our services include:
- Consultation: Collaborating with you to understand your needs and develop a solution that meets them.
- Design: Utilizing advanced design tools to create a cleanroom that integrates seamlessly with your manufacturing process.
- Manufacturing: Building your cleanroom with precision and care to ensure quality and compliance.
- Installation: Ensuring a smooth installation process with minimal disruption to your operations.
- Certification: Assisting with the certification process to verify that your cleanroom meets all necessary standards.
- Maintenance: Offering maintenance services to keep your cleanroom in optimal condition.
Why Choose G-Con
Our commitment to quality, innovation, and client satisfaction makes G-Con the preferred choice for electronics cleanroom solutions. With our prefabricated cleanrooms, you benefit from reduced construction time, flexibility, and adherence to the highest industry standards. Contact us to discover how we can support your cleanroom needs.