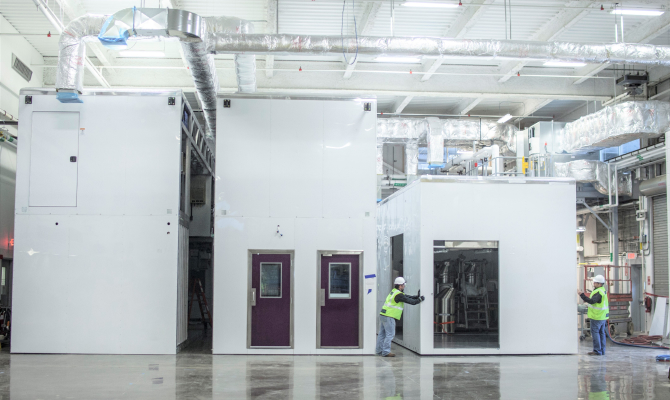
May 05, 2025
Discover the Efficiency and Compliance of Turnkey Cleanrooms
Our turnkey cleanroom solutions deliver a new era of operational efficiency, where rapid deployment meets uncompromised quality. Designed to eliminate lengthy construction delays, our modular systems provide a fully pre-engineered, validated environment that ensures your facility remains at the forefront of innovation and regulatory excellence.
By choosing our solutions, you benefit from state-of-the-art design that meets stringent standards such as ISO 14644 for air cleanliness, GMP for pharmaceutical integrity, and FDA 21 CFR Part 11 for secure electronic records. Enhanced further with USP 797 and 800 compliance, these facilities guarantee precise aseptic processing and contaminant control.
Our cleanrooms are essential for high-stakes industries including pharmaceutical and biotechnological manufacturing, semiconductor and electronics assembly, and aerospace precision production. Built with advanced Building Management Systems (BMS), Environmental Monitoring Systems (EMS), and integrated IoT-driven automation, our systems empower you with real-time monitoring and data analytics for seamless operational control.
Offering rapid deployment and expansion capabilities, our modular solutions reduce overall costs while adapting to your evolving production needs. The prevalidated, scalable configurations minimize on-site installation time, providing you with a future-proof controlled environment that is as efficient as it is compliant.
At G-CON, our expertise in modular cleanroom technology transforms conventional standards into dynamic, turnkey innovations that drive your operational success. Experience a new benchmark in controlled environment manufacturing—engineered for precision, validated for compliance, and optimized for your growth.
What Advantages Do Turnkey Cleanrooms Offer?
Accelerated Deployment & Operational Readiness
We deliver pre-engineered, validated modular cleanrooms that slashes installation time from years to months. Our systems come fully integrated and ready for immediate deployment—ideal for industries demanding rapid market entry, whether in pharmaceuticals for aseptic processing, semiconductors for particulate control, or aerospace for precision manufacturing.
Cost Efficiency & Predictable Budgeting
By applying fixed-cost designs and minimizing on-site labor, we eliminate unexpected expenses associated with design revisions or regulatory delays. Rigorous Factory Acceptance Testing confirms performance before shipment, ensuring a seamless installation that controls costs and maximizes investment.
Regulatory Compliance & Quality Assurance
Our cleanrooms meet ISO 14644, GMP, FDA 21 CFR Part 11, and USP 797/800 requirements. Each unit undergoes strict validation, guaranteeing air cleanliness, robust environmental monitoring, and consistent aseptic conditions.
Scalability & Adaptability
Our modular cleanroom solutions allow you to expand, reconfigure, or relocate as production demands evolve. Easily integrate multiple units to support large-scale operations while adapting to emerging standards without major structural changes.
Integrated Automation & Smart Monitoring
Equipped with advanced BMS, EMS, and IoT automation, our cleanrooms offer real-time control of critical parameters. This intelligent system promotes process stability, enables predictive maintenance, and maintains continuous compliance.
G-CON’s Leadership
With our standardPOD, mobilisPOD, and megaPOD configurations, we redefine cleanroom excellence—delivering dynamic, future-proof environments tailored for high-performance operations.
How Quickly Can Turnkey Cleanrooms Be Deployed?
Accelerating Deployment with Modular Precision
Our turnkey cleanrooms deliver unmatched speed-to-market by eliminating the delays inherent in traditional construction. With fully engineered and prefabricated modules, these systems arrive validated and ready for integration—shifting deployment timelines from years to mere months. This expedited setup is crucial when operational readiness is non‐negotiable in high-stakes industries.
Streamlined Deployment Process: From Factory to Operation
We follow a rigorous, sequential process to ensure rapid implementation:
- Design & Engineering (2–4 Weeks): Standardized, prevalidated configurations eliminate costly custom work.
- Off-Site Fabrication (8–12 Weeks): Factory-controlled manufacturing guarantees precision and compliance.
- Factory Acceptance Testing (2 Weeks): Pre-delivery validation removes on-site commissioning delays.
- Delivery & Installation (2–4 Weeks): Preassembled modules are integrated seamlessly into your facility.
- Site Acceptance Testing (1–2 Weeks): Final verification confirms immediate operational readiness.
Key Drivers of Rapid Implementation
Our modular approach—and commitment to regulatory pre-validation—ensures that complexity is minimized from the start:
- Prefabrication & Standardization: Reducing on-site coordination simplifies construction.
- Minimal Infrastructure Demands: Plug-and-play utility connections accelerate installation.
- Built-In Regulatory Compliance: Validation against ISO 14644, GMP, and FDA 21 CFR Part 11 ensures that every unit meets stringent standards before reaching your site.
- Integrated Automation: Advanced BMS and EMS systems provide instantaneous control over environmental parameters.
Business Impact: A Strategic Edge
Speed in deployment translates directly into accelerated production, minimized downtime, and predictable cost structures. Industries—from biopharmaceuticals to semiconductor manufacturing and aerospace—capitalise on rapid scalability, enhanced cost control, and unwavering regulatory adherence.
G-CON’s Modular Excellence
Our standardPOD, mobilisPOD, and megaPOD series set a new standard in quick-turn deployment. With pre-engineered units and integrated automation, we provide operational environments that are not only compliant and precise but also poised for immediate performance.
Why Is Compliance Critical for Turnkey Cleanrooms?
Regulatory Pillars for Operational Excellence
Compliance is the backbone of our modular cleanroom solutions. In highly regulated sectors, maintaining stringent air cleanliness, contamination control, and operational safety is essential. Our approach aligns with globally recognized standards—ISO 14644 defines air cleanliness and particulate limits; GMP ensures robust pharmaceutical production; FDA 21 CFR Part 11 secures electronic records; and USP 797/800 uphold sterile compounding and hazardous drug handling.
Integrated Quality Assurance
Our systems undergo rigorous testing to guarantee peak performance. Pre-deployment Factory Acceptance Testing confirms that each prevalidated module meets all regulatory criteria. Upon installation, Site Acceptance Testing verifies real-time parameters including airflow dynamics and pressure stabilization. Continuous environmental monitoring using advanced EMS ensures that your operating environment remains within prescribed limits. Simultaneously, our automated Building Management Systems maintain precise control over temperature and contamination, establishing a seamless bridge between design and day-to-day operations.
Impact on Your Operations
Adhering to these regulatory frameworks directly enhances process stability and minimizes production variability. Ensuring contamination prevention not only safeguards the quality of your products but also streamlines audits and regulatory inspections, preventing costly delays. This multidisciplinary strategy supports efficient, scalable operations, making your facility responsive to emerging industry trends and standards.
Our Commitment
At G‑CON, our standardPOD, mobilisPOD, and megaPOD cleanroom configurations are engineered for non‐compromise compliance. By embedding advanced automation and real-time monitoring into every module, we empower you with a future‑proof environment designed for lasting operational success.
How Can Turnkey Cleanrooms Be Customized?
Tailoring Solutions for Your Industry’s Demands
Our modular cleanroom systems are engineered to meet the precise technical and regulatory requirements across high-stakes sectors such as pharmaceuticals, biotechnology, semiconductors, and aerospace. By aligning with industry standards like ISO 14644, GMP, FDA 21 CFR Part 11, and USP 797/800, we empower your operations with environments that excel in both performance and compliance.
Customization Options Driven by Innovation
Optimized Airflow and Filtration
- Achieve targeted air cleanliness with configurations ranging from ISO 5 to ISO 8.
- Select between unidirectional (laminar) or non-unidirectional airflow to maintain strict contamination control.
- Customize HEPA and ULPA filtration systems to match particulate sensitivity specific to your processes.
Flexible Modular Layout and Scalability
- Adapt and expand using interconnected POD configurations that grow with your operation.
- Incorporate high-bay designs to support large equipment and streamline high-volume processes.
- Design your facility layout to facilitate seamless integration, ensuring minimal disruption during expansion.
Integrated Environmental Control and Automation
- Benefit from advanced BMS and EMS solutions that deliver precise temperature, humidity, and pressure regulation.
- Implement IoT-enabled real-time monitoring for proactive predictive maintenance.
- Ensure continuous compliance and operational stability through automated environmental oversight.
Process-Specific Adaptations
- Configure aseptic processing suites that perfectly align with sterile manufacturing protocols.
- Build specialized containment areas to adhere to hazardous material standards and USP 800 requirements.
- Include custom pass-throughs, airlocks, and gowning spaces tailored to your production workflow.
Advanced Material Selection and Surface Treatments
- Utilize non-shedding, GMP-compliant panels and ESD-safe flooring, designed to support your quality standards.
- Apply chemical-resistant coatings that enhance durability and longevity in demanding environments.
Expertise in Customization
With our standardPOD, mobilisPOD, and megaPOD solutions, we deliver environments that are uniquely designed for your operational requirements. Every system is prevalidated, configurable, and optimized for immediate integration into your workflow—ensuring that your facility remains efficient, compliant, and ready for future growth.
What Are the Cost Benefits of Turnkey Cleanrooms?
Turnkey cleanrooms deliver a measurable reduction in upfront capital expenditure through off-site prefabrication and pre-engineered modular designs. Our modular POD systems are pre-assembled and validated to cut initial investment by approximately 25–30% compared to traditional builds.
Predictable budgeting is achieved with fixed pricing models and factory-controlled quality assurance, minimizing the need for on-site modifications and unexpected costs. By requiring minimal site preparation, our systems provide financial consistency that supports streamlined project planning.
Accelerated deployment is another strategic advantage. While conventional cleanroom projects span 12–24 months, our modular POD® Cleanrooms become operational within 3–6 months. This rapid setup initiates production sooner, reduces downtime, and lowers opportunity costs—critical factors in industries such as biopharmaceuticals, semiconductors, and aerospace.
Long-term ROI is further enhanced by energy-efficient HVAC and filtration systems that reduce utility expenses. Integrated automation via advanced BMS and EMS optimizes environmental control, ensuring both operational savings and scalable expansion without major structural modifications.
Our cost-effective solutions—encompassing standardPOD, mobilisPOD, and megaPOD configurations—provide a competitive, regulatory-compliant alternative that empowers your organization to maximize returns while achieving enduring operational excellence.
How Do Turnkey Cleanrooms Contribute to Sustainability?
Reducing Environmental Impact with Modular Cleanrooms
Our modular cleanrooms dramatically cut material waste and carbon emissions through precise off-site production, energy-smart design, and sustainable material use. Factory-controlled construction minimizes excess waste, while prevalidated components lower onsite disruptions. By adopting recyclable materials such as aluminum frames and non-shedding panels, our systems support a circular economy in controlled environments.
Sustainability in Practice
Efficient HVAC and filtration systems, designed for ISO 14644 compliance, optimize energy consumption without compromising air purity. Advanced controls adjust temperature, humidity, and airflow in real time, ensuring minimal energy use and robust environmental oversight. Integrated smart systems continuously monitor these parameters, fostering proactive maintenance and cost-effective operations.
Modular scalability also plays a critical role. Expandable configurations and relocatable units allow your facility to adapt without costly reconstruction, extending the lifecycle of your investment while reducing the environmental footprint.
Aligning with Global Sustainability Standards
Our cleanroom solutions align with ISO 14001 and ISO 50001 frameworks, aiding your organization in meeting environmental management and energy efficiency targets. Through the fusion of sustainable design and rigorous quality control, we support your commitment to operational excellence and corporate responsibility.
G‑CON’s standardPOD, mobilisPOD, and megaPOD cleanrooms embody future‑focused sustainability, providing you with a dynamic, compliant, and eco‑conscious manufacturing environment.
Contact G-CON Today
Partner with the Leader in Modular Cleanroom Innovation
At G‑CON, we redefine cleanroom manufacturing by integrating high-performance, prefabricated POD systems that accelerate your facility’s setup while ensuring uncompromised regulatory standards. Our advanced standardPOD, mobilisPOD, and megaPOD configurations are meticulously engineered for industries such as pharmaceuticals, biotechnology, semiconductors, and aerospace. We combine rapid, off-site fabrication with robust process validation to deliver operational environments that are efficient, compliant, and ready for future demands.
Experience accelerated facility readiness as our systems reduce installation timelines from years to months. We ensure every solution meets rigorous standards including ISO 14644, GMP, FDA 21 CFR Part 11, and USP 797/800, all while integrating state-of-the-art environmental monitoring via smart BMS and EMS. This approach not only minimizes on-site labor and unforeseen costs, but also supports scalable and adaptable production setups.
Our expert team collaborates with you to design a controlled environment tailored to your operational needs. From precise airflow optimization and high-bay configurations to integrated IoT-enabled monitoring, our solutions deliver superior quality and sustainable performance.
- Accelerated build and installation timelines
- Rigorous regulatory compliance and validation
- Scalable, flexible designs that evolve with your production
- Integrated automation for real-time environmental control
- Cost-effective, off-site prefabrication and process assurance
Discover how our intelligent, modular cleanrooms empower your organization to achieve operational excellence and strategic growth.
Which Industries Rely on Turnkey Cleanrooms?
Our turnkey cleanrooms serve sectors that demand precise environmental control, rigorous regulatory adherence, and swift facility setup. These solutions streamline operations by ensuring robust contamination control, process stability, and comprehensive compliance.
Pharmaceutical & Biotechnology
Pharmaceutical and biotech operations depend on our GMP-compliant, prevalidated cleanrooms to support aseptic manufacturing, cell and gene therapies, and vaccine production. Our units deliver ISO 14644–certified spaces with integrated BMS and EMS, enabling real-time environmental oversight that accelerates facility activation.
Semiconductor & Electronics
For microelectronics and semiconductor fabrication, our systems provide ultra-clean environments that safeguard sensitive components against particulate interference. With classifications from ISO 5 to ISO 8 and built‐in ESD safeguards, our scalable designs evolve with production demands.
Aerospace & Defense
Aerospace manufacturing benefits from high-bay designs that facilitate precision assembly and maintain material integrity. Our solutions offer meticulous particulate control and expedited setup, essential for critical defense applications and satellite production.
Food & Beverage
In food processing, controlled cleanroom environments support hygienic production and meet stringent safety criteria. Our systems integrate seamlessly with existing lines while conforming to FDA and HACCP guidelines, ensuring prolonged product integrity.
G‑CON’s Modular Advantage
Our standardPOD, mobilisPOD, and megaPOD configurations epitomize rapid, regulatory-ready deployment. Designed for versatility and efficiency, these solutions provide a dynamic controlled environment that empowers your organization to excel in production and innovation.
How Is Compliance Achieved in Turnkey Cleanrooms?
G‑CON achieves strict compliance through a cohesive integration of regulatory standards, robust quality frameworks, and intelligent automation. Our modular cleanrooms meet international benchmarks including ISO 14644 for air cleanliness, GMP protocols ensuring manufacturing integrity, FDA 21 CFR Part 11 for secure electronic records, and USP guidelines for sterile compounding. These standards form the cornerstone of our operational excellence.
Regulatory Frameworks and Quality Assurance
Every system undergoes comprehensive pre-deployment validation. Factory Acceptance Testing (FAT) confirms that environmental controls, filtration systems, and integrated automation meet all statutory requirements before delivery. Upon installation, Site Acceptance Testing (SAT) rigorously verifies airflow, pressure differentials, and environmental monitoring performance. Continuous EMS safeguards operational conditions by tracking particulate levels, temperature, and humidity in real time. Our advanced Building Management Systems actively control these variables to prevent cross‐contamination and ensure consistent compliance.
Certification and Automated Monitoring
Our process includes thorough HEPA/ULPA filtration efficiency assessments, detailed airflow visualization studies, and systematic pressure analytics. Automated data logging produces audit‐ready records that support regulatory inspections with precision. Each G‑CON configuration—whether standardPOD, mobilisPOD, or megaPOD—is built with prevalidated designs that align with evolving industry mandates. This seamless integration of quality assurance, smart monitoring, and proactive management ensures that our solutions consistently exceed compliance requirements while adapting to future challenges.
By employing advanced analytics and continuous improvement practices, our systems dynamically adjust to regulatory updates and operational demands. Every component is meticulously engineered and subject to periodic revalidation, ensuring long‐term performance and compliance integrity. Our committed approach streamlines inspections and minimizes downtime, delivering enduring operational benefits while supporting sustainable growth. This proactive methodology furnishes your facility with continuous competitive advantage.
What Customization Options Exist for Turnkey Cleanrooms?
Tailored Cleanroom Configurations for Industry-Specific Needs
Our modular cleanrooms empower your organization with adaptable, high-performance environments designed to meet the unique demands of pharmaceuticals, biotechnology, semiconductors, and aerospace. These solutions combine advanced process optimization with rigorous regulatory adherence, delivering scalable and compliant systems that integrate seamlessly into your operational workflow.
Key Customization Options
Cleanroom Airflow and Filtration
Experience precise control over particulate levels with designs compliant from ISO 5 to ISO 8. Choose between unidirectional and non-unidirectional airflow configurations that suit your contamination control requirements. Our engineered HEPA/ULPA filtration systems precisely manage airborne particle concentrations to support stringent quality standards.
Scalability and Layout Flexibility
Our pre-engineered POD configurations enable phased facility expansions without disrupting ongoing operations. Interconnected suites support multi-stage manufacturing while high-bay options accommodate larger equipment and vertical process integration, ensuring your facility evolves in step with production needs.
Environmental Control and Automation
Benefit from integrated Building Management and Environmental Monitoring Systems that continuously track temperature, humidity, and pressure differentials. IoT-enabled solutions facilitate predictive maintenance and allow immediate adjustments to maintain process stability and consistency.
Process-Specific Adaptations and Surface Engineering
Customize your space with dedicated aseptic processing suites, containment areas for hazardous materials, and purpose-built airlocks and gowning spaces. High-performance materials, including non-shedding panels, ESD-safe flooring, and chemical-resistant coatings, reinforce durability under demanding cleaning protocols.
Our standardPOD, mobilisPOD, and megaPOD solutions provide you with flexible, futureproof environments engineered for operational excellence and rapid scalability without compromise.
How Do Turnkey Cleanrooms Promote Sustainability?
Our modular cleanroom solutions redefine environmental responsibility through precise, off-site fabrication and innovative design. Preassembled in controlled facilities, these units ensure exact material usage and markedly reduce on-site waste. By incorporating recyclable aluminum frames and low-emission wall panels, we minimize resource consumption while cutting carbon emissions.
Energy Efficiency & Smart Environmental Controls
Engineered with advanced HVAC systems that meet rigorous ISO 14644 standards, our cleanrooms feature energy-efficient HEPA/ULPA filtration that maximizes particulate control with minimal energy use. Automated Building and Environmental Management Systems actively adjust temperature, humidity, and airflow in real time, delivering optimized performance and reducing operational energy demands.
Scalable, Future-Proof Design
Our modular approach empowers your organization with flexible configurations that adapt as production needs evolve. These relocatable units eliminate the need for extensive new construction, preserving your environmental footprint over the long term. With design principles focused on durability and resource conservation, our cleanroom solutions extend operational lifespan and offer substantial lifecycle cost savings.
Commitment to Environmental Excellence
Aligned with global standards such as ISO 14001 and ISO 50001, our solutions integrate sustainable design with robust regulatory compliance. This integrated strategy supports precise energy management and strategic waste reduction, helping you meet both corporate sustainability goals and stringent industry requirements. Every prevalidated unit is a testament to our dedication to reducing environmental impact while driving operational excellence.
Through smart design, energy efficiency, and scalable modularity, our cleanrooms not only enhance your production capabilities but also contribute significantly to a sustainable future. Embrace a solution that supports your operational growth and environmental stewardship simultaneously.
What Are the Financial Advantages of Turnkey Cleanrooms?
Lower Initial Investment through Modular Construction
Our turnkey cleanrooms cut your upfront capital costs by implementing off-site prefabrication and prevalidated modular designs. G‑CON’s modular POD® Cleanrooms arrive fully assembled, reducing initial expenses by approximately 25–30% compared to conventional builds.
Budget Stability and Fixed-Cost Design
Traditional projects often face unexpected changes that inflate budgets. With our fixed-cost pricing model, factory-controlled quality assurance, and minimal site modifications, your financial planning becomes predictable and efficient, sparing your organization from variable expenses.
Accelerated Deployment and Enhanced ROI
Accelerated installation is vital in sectors such as biopharmaceuticals, semiconductor manufacturing, and aerospace. While traditional cleanroom build times extend up to 24 months, our modular systems are operational in just 3–6 months. This rapid setup enables faster production starts, reduces downtime, and minimizes opportunity costs, thus hastening your return on investment.
Long-Term Efficiency and Adaptability
Beyond initial savings, our solutions deliver ongoing financial advantages. Energy-efficient HVAC and state-of-the-art filtration systems lower your utility bills, while integrated automation within our BMS and EMS safeguards operational performance. The inherent scalability of our designs ensures your facility can expand as production demands grow without incurring major retrofitting costs.
Comparative Advantage
A clear comparison reveals that turnkey modular cleanrooms demand lower upfront capital, minimize labor expenses, and offer prevalidated compliance compared with traditional construction methods. G‑CON’s standardPOD, mobilisPOD, and megaPOD series provide a cost-effective, scalable, and regulation-ready solution that supports your operational excellence.
What Is the Deployment Speed of Turnkey Cleanrooms?
Our modular cleanrooms are engineered to eliminate the delays of conventional construction, transforming setup time from years to just months. Designed with fully pre-engineered, validated modules, they are delivered ready for rapid integration—ensuring your facility is up and running quickly while meeting strict regulatory standards.
Streamlined Process for Rapid Deployment
The deployment process follows a concise, five-phase sequence:
- Design & Engineering (2–4 Weeks): Our standardized configurations remove the need for extensive custom work.
- Off-Site Fabrication (8–12 Weeks): Factory-controlled production guarantees precision and robust compliance.
- Factory Acceptance Testing (2 Weeks): Prevalidation at the manufacturing site minimizes on-site delays.
- Delivery & Installation (2–4 Weeks): Preassembled modules arrive at your site, ready for immediate integration.
- Site Acceptance Testing (1–2 Weeks): Final verification confirms operational readiness with real-time environmental validation.
Key Accelerators
Several factors drive our unrivaled deployment speed:
- Pre-Engineered Standardization: Modular designs reduce the need for complex on-site construction.
- Minimal Infrastructure Demands: Plug-and-play utility connections streamline installation.
- Regulatory Pre-Validation: Every unit is prevalidated against ISO 14644, GMP, and FDA 21 CFR Part 11, ensuring immediate compliance.
- Integrated Automation: Smart Building Management (BMS) and Environmental Monitoring Systems (EMS) provide instant operational control.
Business Impact
Faster deployment means you can begin production sooner, reduce downtime, and achieve predictable budgeting. Industries—from biopharmaceuticals to semiconductor manufacturing and aerospace—benefit from rapid scalability, fixed-cost solutions, and streamlined approvals.
G‑CON’s standardPOD, mobilisPOD, and megaPOD configurations set the industry benchmark. With our preassembled, automation-integrated, and regulation-ready cleanrooms, your facility can be operational within weeks—empowering your operations with speed and precision.