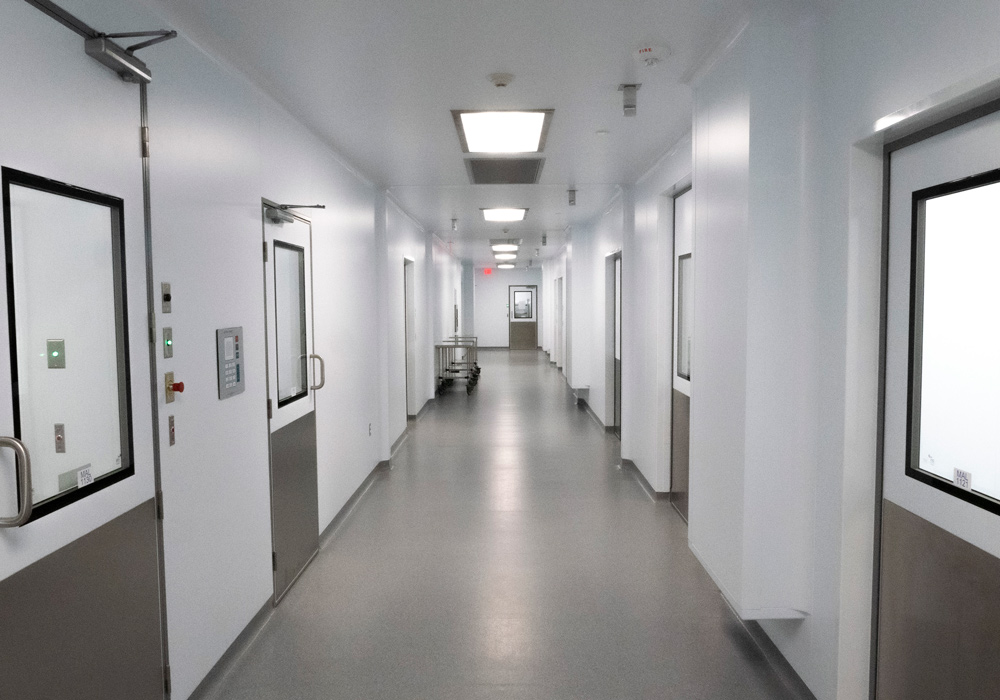
Dec 04, 2023
G-CON Cleanrooms for Pharmaceutical Manufacturing
Understanding the Vital Role of Cleanrooms in Pharmaceutical Manufacturing
Pharmaceutical cleanrooms are specialized environments with controlled levels of contamination to ensure the sterility and integrity of pharmaceutical products. These environments are meticulously designed to maintain low levels of particulates, such as dust, airborne microbes, and aerosol particles. At G-CON, we recognize that the core function of a cleanroom is to provide a contamination-free space where sensitive pharmaceutical processes can occur without compromising product quality or patient safety.
Ensuring Product Safety and Efficacy
Cleanrooms are the heart of quality assurance in the pharmaceutical industry. By adhering to stringent standards, such as ISO 14644-1 and Good Manufacturing Practices (GMP), our cleanrooms ensure that products meet the highest safety and efficacy standards. The controlled environment minimizes the risk of contamination, which is crucial for products that must be free from microbes and particulates.
Impact on Quality and Compliance
The design and operation of cleanrooms directly impact product quality and regulatory compliance. With real-time environmental monitoring systems and advanced filtration technologies, such as HEPA and ULPA filters, we ensure that our cleanrooms not only meet but exceed global standards. This commitment to excellence is reflected in every aspect of our cleanroom solutions, from airflow patterns to material selection.
The G-CON Advantage: Modular Cleanroom Solutions
Our modular cleanroom approach is at the forefront of innovation. G-CON’s prefabricated cleanrooms, such as the standardPOD, mobilisPOD, and megaPOD, offer flexibility, scalability, and faster deployment compared to traditional construction. With features like Factory Acceptance Testing and integration of Building Management Systems (BMS) and Environmental Monitoring Systems (EMS), we provide cleanrooms that are not only compliant with global standards but also tailored to your specific manufacturing needs.
Understanding ISO Classifications in Pharmaceutical Cleanrooms
When you’re navigating the complex world of pharmaceutical cleanrooms, understanding ISO classifications is paramount. These classifications, ranging from ISO 5 to ISO 9 as per the ISO 14644-1 standard, dictate the permissible particle count in the air, directly impacting the sterility of your pharmaceutical products. At G-CON, we ensure that our modular cleanrooms meet these stringent classifications, providing environments that are conducive to the high standards required for pharmaceutical manufacturing.
The Influence of GMP Guidelines on Cleanroom Design
Good Manufacturing Practice (GMP) guidelines are the bedrock of pharmaceutical production, influencing every aspect of cleanroom design and operation. These guidelines ensure that products are consistently produced and controlled according to quality standards. Our cleanroom solutions are designed with GMP principles at their core, ensuring that your operations are compliant and your products are of the highest quality.
The Role of Regulatory Bodies in Cleanroom Standardization
Regulatory bodies like the FDA play a critical role in cleanroom standardization, setting the bar for product safety and efficacy. Their regulations are designed to protect consumers and ensure that pharmaceutical products are free from contamination. By aligning with these regulations, our cleanrooms help you navigate the complexities of compliance, making the certification process smoother and more predictable.
Achieving Compliance Through Classification Understanding
Grasping the nuances of cleanroom classifications and standards is not just about meeting regulatory requirements; it’s about exceeding them. At G-CON, we believe that a deep understanding of these classifications is a stepping stone to achieving and maintaining compliance. Our expertise in modular cleanroom design and operation positions us to guide you through the intricacies of these standards, ensuring that your facility is not just compliant, but also operates at the pinnacle of efficiency and safety.
Key Design Features of Pharmaceutical Cleanrooms
In the realm of pharmaceutical manufacturing, the design of a cleanroom is critical to its function. Our modular cleanrooms at G-CON are engineered with precision to ensure a controlled environment that meets the stringent requirements of the pharmaceutical industry. The critical design features include HEPA and ULPA filtration systems to maintain particulate-free air, airlock systems to prevent cross-contamination, and materials that are non-particulate shedding and resistant to rigorous cleaning protocols.
Material Selection for Cleanroom Integrity
The integrity and compliance of a cleanroom are significantly influenced by the materials used in its construction. We select non-shedding panels and impervious surfaces that withstand advanced surface disinfection methods. This careful selection minimizes the risk of contamination and ensures that our cleanrooms meet global standards, including ISO 14644-1 and cGMP.
Layout Considerations for Optimal Contamination Control
The layout of a cleanroom is meticulously planned to optimize workflow efficiency and minimize contamination risks. Our designs consider the placement of equipment, personnel movement, and the segregation of areas to control bioburden effectively. By incorporating laminar airflow patterns and pressurization, we create environments that support aseptic processing.
Streamlining Construction with Modular Design
G-CON’s modular cleanroom solutions revolutionize the construction process. Our prefabricated POD® Cleanrooms are designed for rapid deployment and scalability, allowing for a seamless integration into existing facilities or the creation of new ones. This approach not only streamlines the construction process but also offers the flexibility to adapt to the evolving needs of the pharmaceutical industry.
Essential Air Filtration Systems for Pharmaceutical Cleanrooms
At G-CON, we recognize that air purity is the lifeblood of a pharmaceutical cleanroom. To maintain this purity, advanced air filtration systems are non-negotiable. These systems are designed to remove contaminants from the air, ensuring that the environment within the cleanroom meets the rigorous standards required for pharmaceutical manufacturing.
Functionality of HEPA and ULPA Filters
High-Efficiency Particulate Air (HEPA) filters and Ultra-Low Particulate Air (ULPA) filters are at the forefront of our air filtration solutions. HEPA filters are capable of trapping 99.97% of particles that are 0.3 microns in diameter, while ULPA filters go even further, capturing 99.999% of particles down to 0.12 microns. These filters are critical in maintaining the ISO 5-9 cleanliness levels required in sensitive pharmaceutical processes.
Best Practices for Air Filtration Maintenance
To ensure the continued effectiveness of these filtration systems, we advocate for a strict maintenance regimen. This includes regular checks for filter integrity, timely replacement, and adherence to the cleanroom’s specific operational protocols. Our team provides comprehensive training and support to ensure that you’re equipped to maintain these systems effectively.
Integration of Advanced Filtration in Modular Solutions
Our modular cleanroom solutions come equipped with these advanced filtration technologies. By integrating real-time environmental monitoring systems and automation, we ensure that air quality is consistently maintained at optimal levels. This integration is a testament to our commitment to delivering turnkey solutions that meet the highest standards of air purity in the pharmaceutical industry.
Selecting Cleanroom Furniture and Tools: A Guide for Technicians and Managers
When outfitting a pharmaceutical cleanroom, the selection of furniture and tools is critical. At G-CON, we understand that every item introduced into a cleanroom must meet stringent criteria to minimize contamination risks. Our furniture and tools are designed to be functional, durable, and, most importantly, compliant with cleanroom standards.
Criteria for Cleanroom-Compatible Equipment
The primary criteria for selecting furniture and tools for cleanrooms include material compatibility, ease of cleaning, and resistance to sterilization processes. We ensure that all our equipment is made from non-particulate shedding materials and can withstand frequent disinfection. This careful selection process significantly reduces the risk of contamination and supports your compliance with ISO and GMP standards.
Impact of Equipment on Contamination Risk
The equipment choices you make can directly influence the contamination risk within your cleanroom. Our modular furniture is engineered to integrate seamlessly with our cleanroom designs, ensuring that there are no gaps or hard-to-clean areas where contaminants could accumulate. By choosing G-CON’s solutions, you’re opting for a cleanroom environment that prioritizes sterility at every turn.
Cleanroom-Compatible Storage Solutions
Storage solutions in a cleanroom must be designed to prevent contamination while maximizing space efficiency. Our storage units are constructed with smooth, impervious surfaces that are easy to clean and maintain. With G-CON’s modular approach, we provide storage solutions that can be customized to fit the unique needs of your cleanroom operations, enhancing overall functionality and workflow efficiency.
Implementing Effective Training Protocols for Cleanroom Personnel
At G-CON, we emphasize the importance of comprehensive training protocols for cleanroom personnel. These protocols are designed to ensure that every individual who enters the cleanroom is well-versed in the practices that maintain its integrity. Our training programs cover a range of essential topics, from understanding the principles of contamination control to the proper use of cleanroom equipment and documentation procedures.
Gowning Procedures: The First Line of Defense Against Contamination
Gowning procedures are a critical component of our training protocols. They serve as the first line of defense against contamination, creating a barrier between the cleanroom environment and potential contaminants. We instruct personnel on the correct method to don cleanroom garments, which includes gowning in a specific sequence to minimize the risk of contamination.
Best Practices for Personnel Flow Management
Managing the flow of personnel in and out of the cleanroom is crucial for maintaining a contamination-free environment. We advocate for best practices that include controlled entry and exit points, staggered access to prevent overcrowding, and clear demarcation of clean and dirty areas. Our modular cleanroom designs facilitate these best practices by incorporating features such as gowning anterooms and material pass-throughs.
G-CON’s Approach to Personnel Protocol in Cleanroom Design
Our approach to cleanroom design at G-CON includes careful consideration of personnel protocols. We understand that the behavior and practices of personnel are as important as the physical design of the cleanroom itself. Therefore, our designs are tailored to support and reinforce the training protocols, ensuring that personnel can adhere to the highest standards of cleanroom operation.
Adhering to Cleaning and Disinfection Protocols in Cleanrooms
Maintaining the sterility of pharmaceutical cleanrooms is paramount, and at G-CON, we understand that the selection of cleaning agents and disinfectants is critical. Our protocols specify the use of agents that are effective against a broad spectrum of microorganisms and are compatible with the materials used in cleanroom construction.
Frequency of Cleanroom Cleaning and Disinfection
Regular cleaning and disinfection are essential to maintain the required cleanliness standards. The frequency of these procedures is determined by the cleanroom’s classification and the nature of the pharmaceutical processes conducted within. Our guidelines recommend a cleaning schedule that aligns with industry best practices and regulatory requirements, ensuring that your cleanroom remains compliant and contamination-free.
Validation of Cleaning Effectiveness
To validate the effectiveness of cleaning protocols, we employ various methods, including microbial testing and particle counting. These validation processes are integral to our quality assurance program, providing you with the confidence that the cleanroom environment meets all necessary standards.
G-CON’s Modular Cleanrooms: Designed for Easy Maintenance
Our modular cleanrooms are designed with ease of maintenance in mind. The materials and surfaces used in our POD® Cleanrooms allow for efficient cleaning and disinfection, reducing downtime and ensuring that your operations can resume promptly. With G-CON’s modular solutions, you’re equipped with a cleanroom that not only meets but exceeds the rigorous demands of pharmaceutical manufacturing.
Precision Environmental Control in Cleanrooms
Maintaining precise environmental conditions is crucial for the integrity of pharmaceutical processes. At G-CON, our cleanrooms are equipped with advanced environmental control systems that meticulously regulate temperature and humidity. This level of control is essential for ensuring product stability and adherence to stringent industry standards.
Advanced Monitoring Systems for Particulate Tracking
To safeguard the sterility of our cleanrooms, we utilize state-of-the-art monitoring systems capable of detecting even the most minute particulate levels. These systems provide real-time data, allowing for immediate corrective actions if deviations from the prescribed conditions occur.
Data Logging: The Backbone of Environmental Monitoring
Data logging plays a pivotal role in environmental monitoring, offering a comprehensive record of conditions over time. This historical data is invaluable for trend analysis, troubleshooting, and proving compliance during audits. Our cleanrooms feature integrated data logging systems that ensure a robust and retrievable data trail.
G-CON’s Design for Optimal Environmental Monitoring
Our commitment to excellence is reflected in the design of our cleanrooms, which are optimized for environmental monitoring. With features like real-time environmental monitoring systems and advanced filtration, we ensure that you have the tools necessary to maintain an environment that meets the highest standards of cleanliness and control.
Strategic Waste Management in Pharmaceutical Cleanrooms
Effective waste management is a critical component of maintaining the stringent cleanliness standards of pharmaceutical cleanrooms. At G-CON, we implement comprehensive strategies to manage and dispose of waste, ensuring that our cleanrooms remain free of contaminants and safe for all operations.
Handling and Disposal of Hazardous Materials
The handling and disposal of hazardous materials require meticulous attention to detail and adherence to safety protocols. Our procedures ensure that hazardous waste is segregated at the point of generation, contained appropriately, and disposed of following all regulatory guidelines. This minimizes the risk of exposure and contamination, safeguarding both personnel and products.
Recommended Containment Systems for Cleanroom Waste
We recommend containment systems that are designed specifically for cleanrooms, which include sealed waste receptacles and closed transfer systems. These systems are engineered to prevent the escape of contaminants into the cleanroom environment, ensuring that waste is managed without compromising the integrity of the space.
G-CON’s Modular Design and Waste Management Logistics
Our modular cleanroom design incorporates waste management logistics from the outset. We understand that the efficient removal of waste is as important as any other aspect of cleanroom operation. Therefore, our designs include integrated waste management solutions that are easy to use and maintain, ensuring that waste handling is a seamless part of your cleanroom’s workflow.
Implementing In-Process Testing in Cleanrooms
In-process testing is a cornerstone of quality assurance in pharmaceutical cleanrooms. At G-CON, we understand that consistent monitoring throughout the manufacturing process is crucial. Our cleanrooms are equipped with advanced environmental monitoring systems that allow for real-time tracking of particulate levels, temperature, and humidity, ensuring that the conditions necessary for product safety and efficacy are always met.
Conducting Risk Assessments for Product Safety
Risk assessments are integral to our quality control measures. We perform thorough evaluations to identify potential sources of contamination and implement strategies to mitigate these risks. By assessing the workflow, equipment, and personnel practices, we ensure that every aspect of our cleanroom operations upholds the highest safety standards.
The Role of Continuous Improvement
Continuous improvement is embedded in our operational ethos. We regularly review and refine our processes, seeking ways to enhance efficiency and quality. This commitment to excellence means that our cleanrooms are not just compliant with current standards but are also adaptable to future advancements and regulatory changes.
G-CON’s Cleanrooms: A Paradigm of Quality Assurance
Our modular cleanrooms are designed with quality assurance as a priority. From the ground up, every component, from air filtration systems to gowning protocols, supports rigorous quality control measures. By choosing G-CON, you’re selecting a partner that provides an environment where quality is not just a goal but a guarantee.
Criteria for Evaluating Cleanroom Suppliers
As procurement managers and technicians, you’re tasked with the critical responsibility of selecting the right cleanroom solutions that align with your organization’s standards and needs. At G-CON, we recommend evaluating suppliers based on a comprehensive set of criteria:
- Compliance with Global Standards: Ensure the supplier’s products meet ISO and GMP guidelines.
- Quality of Materials: Assess the durability and suitability of materials for sterile environments.
- Design Flexibility: Consider modular designs like our POD® Cleanrooms for scalability and customization.
- Technical Support: Look for suppliers that offer robust customer service and technical assistance.
Impact of Supplier Audits and Certifications
Supplier audits and certifications are pivotal in procurement decisions. They provide assurance that the supplier adheres to industry standards and best practices. At G-CON, our cleanroom solutions are Factory Acceptance Tested and come with certifications that validate their quality and compliance.
Supply Chain Management for Cleanroom Operations
Effective supply chain management is essential for maintaining the integrity of cleanroom operations. It’s important to consider:
- Reliability of Delivery: Consistent and timely delivery is crucial to avoid operational disruptions.
- Quality Assurance: Suppliers should have stringent quality control measures in place.
G-CON’s Commitment to Meeting Procurement Needs
At G-CON, we understand the procurement challenges you face. We strive to meet your needs by providing:
- Custom Cleanroom Solutions: Tailored to specific pharmaceutical processes.
- Comprehensive Support: From design to installation and beyond.
- Regulatory Compliance: Ensuring our products meet the highest standards.
Tailoring Cleanroom Solutions to Your Unique Requirements
At G-CON, we understand that each pharmaceutical operation has unique requirements. That’s why we specialize in customizing cleanroom solutions that align with your specific needs. Whether you require a standardPOD for small-scale production or a megaPOD for large-scale operations, our team is equipped to design a cleanroom that fits your exact specifications.
Installation and Operational Training Support
Our commitment to your success extends beyond the delivery of our cleanrooms. We offer comprehensive support for installation and operational training to ensure that your team is fully prepared to work within these controlled environments. Our training programs cover everything from gowning procedures to environmental monitoring, ensuring that your staff is competent and confident in maintaining the integrity of the cleanroom.
Ensuring Compliance with Industry Standards
Partnering with G-CON means that you’re choosing a cleanroom provider that prioritizes compliance with industry standards. Our cleanrooms are designed and built to meet the stringent requirements of ISO 14644-1, USP 797, USP 800, and cGMP, among others. We stay abreast of regulatory changes to ensure that our solutions are always compliant, giving you peace of mind.
Why G-CON is the Preferred Choice for Cleanroom Solutions
Choosing G-CON for your pharmaceutical cleanroom needs ensures that you’re working with a provider that is committed to quality, compliance, and customer satisfaction. Our prefabricated, modular cleanrooms are not only innovative and efficient but also backed by our dedication to excellence and reliability. Let us be your partner in achieving cleanroom excellence.